Published: September 15, 2023 • Reading time: 12 minutes
Welders Table: The Ultimate Guide to Professional Welding Workstations
Everything you need to know about selecting, building, and optimizing the perfect welders table for your projects
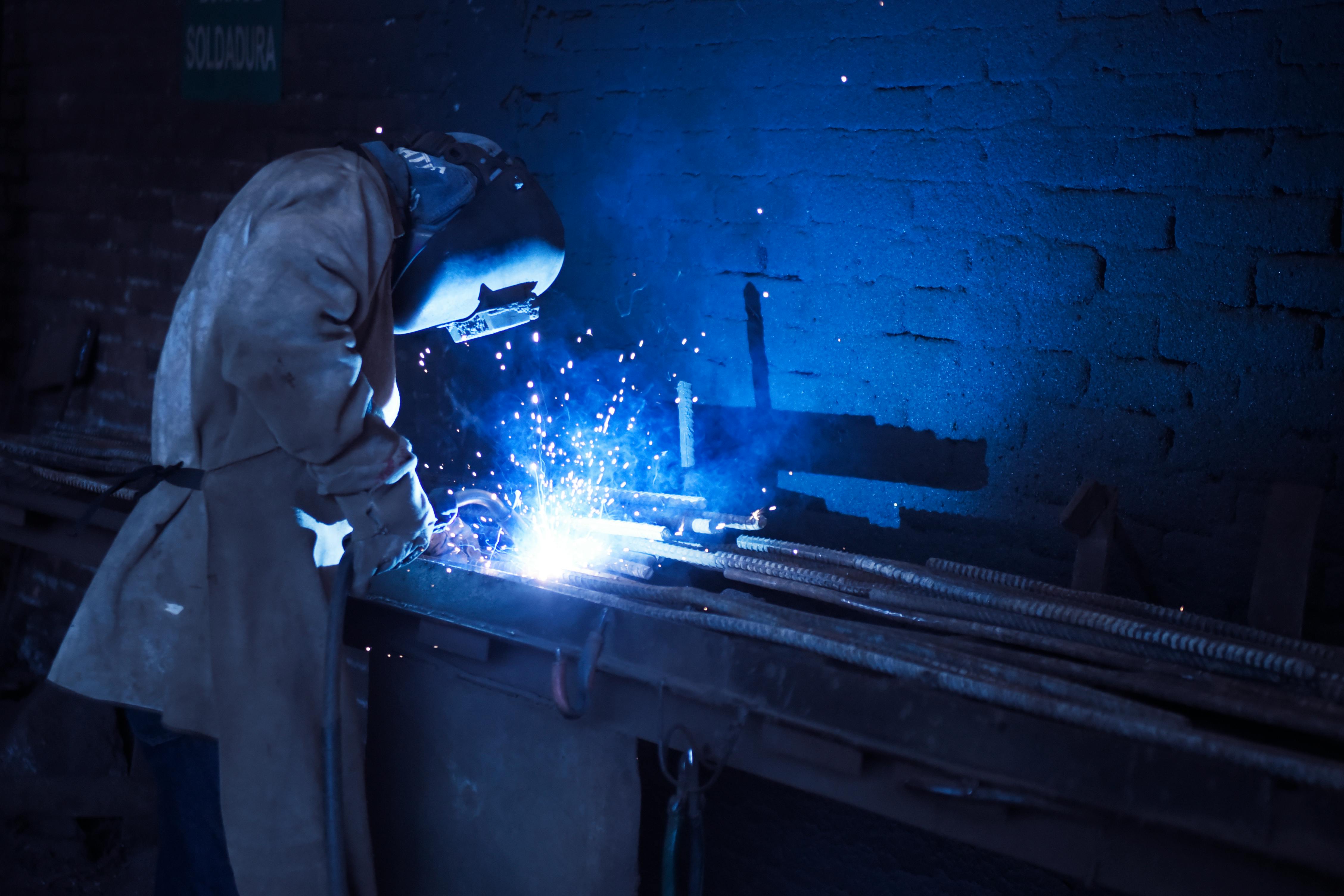
Why Every Welder Needs a Dedicated Welders Table
A quality welders table is more than just a flat surface—it's the foundation of efficient, precise, and safe welding work. Whether you're a professional fabricator or a weekend hobbyist, investing in a proper welders table will significantly improve your welding experience and the quality of your projects. The right welders table provides stability, organization, and functionality that ordinary work surfaces simply cannot match.
Many beginners underestimate the importance of a dedicated welders table, often attempting to weld on whatever flat surface is available. However, a purpose-built welders table offers critical advantages that directly impact your welding quality and efficiency. A professional welders table is designed to withstand the extreme heat, sparks, and physical demands of welding work while providing features specifically tailored to the needs of welders.
In this comprehensive guide, we'll explore everything you need to know about welders tables—from the key features that make a quality welders table, to how to choose the right welders table for your specific needs, and even how to build your own custom welders table. Whether you're in the market for your first welders table or looking to upgrade your existing setup, this article will help you make informed decisions to improve your welding workspace.
Key Benefits of a Professional Welders Table
Precision & Accuracy
A quality welders table provides a perfectly flat, stable surface that helps ensure precise measurements and square joints—essential for professional-quality welding projects.
Enhanced Safety
Purpose-built welders tables are designed with safety in mind, featuring fire-resistant materials, grounding capabilities, and stability that reduces the risk of accidents during welding operations.
Efficiency & Organization
A well-designed welders table includes features for tool organization, material handling, and project positioning that significantly increase workflow efficiency and productivity.
Understanding the Evolution of Welders Tables
The welders table has evolved significantly over time, from simple metal benches to the sophisticated workstations we see today. Early welders tables were little more than heavy steel plates mounted on sturdy legs, providing basic stability but lacking the specialized features found in modern designs. These rudimentary welders tables served their primary purpose but did little to enhance the welder's efficiency or comfort.
Modern welders tables integrate advanced features that address the multifaceted needs of today's welders. Contemporary welders tables often include adjustable height mechanisms, modular fixturing systems, integrated tool storage, and specialized clamping solutions. The evolution of the welders table reflects the industry's increasing focus on precision, ergonomics, and versatility in welding operations.
The latest generation of welders tables also emphasizes adaptability to different welding techniques and projects. Many professional welders tables now feature interchangeable tops, adjustable configurations, and compatibility with a wide range of accessories. This adaptability allows welders to customize their welders table setup for specific projects, maximizing efficiency and precision for each unique welding task.
Essential Features of a Quality Welders Table
When evaluating or designing a welders table, certain features are essential for functionality, durability, and safety. Understanding these critical elements will help you select or build a welders table that meets your specific welding needs and provides long-lasting service in your workshop or fabrication facility.
Material and Construction
The core material of any quality welders table is steel, typically with a thickness between 3/8" to 1" (10mm to 25mm) for the top surface. This thickness ensures that the welders table can withstand the heat, weight, and physical stress of welding operations without warping or degrading. Many professional welders tables use A36 steel or similar grades that offer excellent strength-to-weight ratio and thermal stability.
The supporting structure of a welders table is equally important. Quality welders tables feature robust frames, typically constructed from heavy-gauge steel tubing or structural profiles. These frames give the welders table the stability needed for heavy-duty welding work and often include cross-bracing or gusseted joints for additional rigidity. Some high-end welders tables use specially designed structural elements that optimize weight distribution while maximizing strength.
Surface treatment is another crucial aspect of welders table construction. Many professional welders tables feature ground or machined top surfaces that ensure flatness to within tight tolerances. This precision is essential for accurate fabrication work on your welders table. Additionally, the surface may include a grid of holes, slots, or other fixturing points that enable versatile workholding options on the welders table.
Material Considerations for Different Welders Tables
Welders Table Type | Recommended Materials | Advantages |
---|---|---|
Heavy-Duty Professional | 1" A36 steel plate, 4" steel tube frame | Maximum stability, heat resistance, longevity |
Medium-Duty Workshop | 1/2" steel plate, 3" steel tube frame | Good balance of weight and performance |
Portable Welders Table | 3/8" steel plate, 2" steel tube frame | Reduced weight while maintaining functionality |
Modular System | Nitrided steel plate, precision aluminum profiles | Versatility, corrosion resistance, accuracy |
DIY Welders Table | Salvaged steel plate, structural steel | Cost-effectiveness, customization |
Functional Design Elements
Beyond basic construction, a well-designed welders table incorporates numerous functional elements that enhance its utility for various welding applications. A professional welders table typically features a grid of holes, slots, or fixing points across the surface. These regular patterns allow for the attachment of clamps, stops, and fixtures to the welders table, enabling precise positioning and securing of workpieces during welding operations.
The dimensions of a welders table significantly impact its functionality. While standard welders tables often measure around 4' x 8' (1.2m x 2.4m), sizes vary widely based on intended use. A smaller welders table might be suitable for hobby work, while industrial applications might require much larger welders tables. The height of a welders table is typically between 30" to 36" (76cm to 91cm), though adjustable-height welders tables offer ergonomic advantages for different users and tasks.
Accessibility features are crucial for an effective welders table. Many professional welders tables include side troughs or drawers for tool storage, making essential equipment readily available during welding operations. Some advanced welders tables incorporate integrated power distribution, gas line routing, or exhaust ventilation systems directly into the table structure, creating a comprehensive welding workstation centered around the welders table.
"A properly designed welders table isn't just a tool—it's a complete workspace that enhances every aspect of the welding process."
Safety Considerations for Welders Tables
Safety should be a primary consideration when selecting or designing a welders table. A quality welders table incorporates several safety features that protect both the welder and the workshop environment. Proper grounding is perhaps the most critical safety aspect of a welders table. The metal structure of the welders table should include dedicated grounding points that can be connected to your welding equipment's grounding system, preventing electrical hazards during operation.
Fire resistance is another essential safety feature of professional welders tables. While the steel construction of most welders tables is naturally fire-resistant, additional considerations may include designing the welders table to contain sparks and spatter, or incorporating fire-resistant materials in areas of the welders table where accessories or storage components might be vulnerable to heat damage.
Stability is a fundamental safety aspect of any welders table. A properly designed welders table should remain rock-solid during all welding operations, regardless of the weight or position of the workpiece. Many professional welders tables include leveling feet or anchoring options to ensure the welders table remains stable even on uneven workshop floors, preventing dangerous tipping or movement during critical welding tasks.
Types of Welders Tables for Different Applications
The welding industry offers a variety of welders tables designed for specific applications and environments. Understanding the different types of welders tables available will help you select the option that best fits your particular welding needs, workspace constraints, and budget considerations.
Fixed Professional Welders Tables
Fixed professional welders tables represent the gold standard for permanent welding workstations. These heavy-duty welders tables are designed for continuous use in production environments, featuring thick steel tops (often 1" or more), robust framework, and precision-machined surfaces. Professional welders tables of this category typically remain in a permanent location in the workshop due to their substantial weight, which can exceed 1,000 pounds for larger models.
One key advantage of fixed professional welders tables is their unmatched stability and precision. These welders tables often feature surface flatness tolerances measured in thousandths of an inch, ensuring absolute accuracy for critical fabrication work. Many professional-grade welders tables also include sophisticated fixturing systems with precisely machined holes, slots, or T-tracks that enable complex workholding setups.
While fixed professional welders tables represent a significant investment, their durability makes them cost-effective over time. A quality professional welders table can last decades in a production environment with minimal maintenance, making it the foundation of a professional welding operation. For businesses where welding is a core activity, investing in a premium fixed welders table is often justified by the precision, efficiency, and longevity these workstations provide.
Key Features of Professional Welders Tables
- Precision-machined surfaces
Professional welders tables often feature surface flatness within ±0.005 inches
- Advanced fixturing systems
High-end welders tables include standardized hole patterns for versatile clamping options
- Integrated utilities
Many professional welders tables feature built-in power, air, or gas connections
- Heavy-duty construction
Commercial welders tables can support workpieces weighing several tons
- Modular expansion options
Premium welders tables often support add-on components and extensions
Price range for professional fixed welders tables: $2,000-$10,000+
Modular Welders Tables
Advantages of Modular Welders Tables
- Adaptability to different projects
Modular welders tables can be reconfigured for various welding tasks
- Scalable workspace
Start with a basic welders table and expand as your needs grow
- Standardized fixturing components
Modular welders tables use compatible clamps and accessories across configurations
- Precision construction
Many modular welders tables offer professional-grade accuracy
- Workshop flexibility
Some modular welders tables can be partially disassembled when not in use
Price range for modular welders tables: $1,200-$5,000+
Modular welders tables represent a versatile alternative to fixed workstations, offering adaptability for diverse welding applications. These welders tables typically feature a system of compatible components that can be assembled in various configurations. The core of most modular welders tables is a precision-manufactured table top with a standardized pattern of holes or slots, complemented by a range of interchangeable accessories.
The primary advantage of modular welders tables is their flexibility. Unlike fixed welders tables, modular systems can be expanded, reconfigured, or adapted as project requirements change. Many professional welders appreciate how modular welders tables allow them to create custom setups for specific fabrication tasks, then reconfigure the welders table for an entirely different project the next day.
Brands like Siegmund, Strong Hand Tools, and Certiflat offer sophisticated modular welders table systems with extensive accessories. These systems typically include a range of clamps, squares, stops, and fixturing components that integrate perfectly with the welders table surface. While modular welders tables require a larger initial investment when accessories are included, they provide remarkable versatility that fixed welders tables cannot match.
For workshops that handle diverse projects or have space limitations, a modular welders table often represents the ideal balance of functionality and flexibility. The ability to adapt your welders table configuration to specific project requirements can significantly enhance productivity and precision across a wide range of welding applications.
Portable and Folding Welders Tables
For welders who work in multiple locations or have limited workshop space, portable welders tables offer a practical solution. These lightweight welders tables are designed for mobility while still providing a stable welding surface. Portable welders tables typically weigh between 30 to 100 pounds, making them manageable for transport to different job sites or for storage when not in use.
Folding welders tables represent the most compact option in this category. These welders tables feature hinged designs that allow them to collapse into a flat package for easy transport and storage. While folding welders tables sacrifice some stability and weight capacity compared to fixed models, they provide a reasonable compromise for welders who need mobility or have storage constraints.
Many portable welders tables incorporate clever design features to maximize functionality despite their compact size. Some portable welders tables include adjustable work angles, integrated clamping systems, or tool storage solutions. While they cannot match the precision or capacity of professional fixed welders tables, portable models provide a valuable solution for mobile welders, hobbyists with limited space, or as supplementary workstations in larger shops.
Type of Welders Table | Best For | Key Characteristics | Typical Price Range |
---|---|---|---|
Fixed Professional Welders Table | Production shops, professional fabricators | Maximum stability, precision, and durability | $2,000-$10,000+ |
Modular Welders Table | Versatile workshops, varied projects | Adaptable configurations, expandable system | $1,200-$5,000+ |
Portable Welders Table | Mobile welders, limited space applications | Lightweight, compact, transportable | $200-$800 |
Folding Welders Table | Occasional welders, extremely limited space | Collapsible design, easy storage | $150-$500 |
DIY Custom Welders Table | Budget-conscious welders, specific requirements | Customized features, cost-effective | $300-$1,500 (materials) |
Building Your Own Custom Welders Table
For many welders, building a custom welders table represents an appealing project that allows for personalization while potentially saving money. A DIY welders table can be tailored to your specific workspace, project types, and preferences, creating a workstation that perfectly complements your welding style and requirements.
Planning Your DIY Welders Table
Before cutting any metal for your welders table, careful planning is essential. Begin by determining the primary dimensions of your welders table based on your available space and typical project sizes. Consider the height of your welders table carefully—most welders find that a height between 34" to 38" (86cm to 96cm) provides optimal ergonomics, but this may vary based on your height and the type of welding you typically perform.
Material selection is another critical planning aspect for your DIY welders table. For the top surface, many home builders use 1/4" to 1/2" (6mm to 12mm) steel plate, which balances cost with durability. The supporting structure of your welders table might utilize square steel tubing (typically 2" or larger) or structural steel profiles, depending on your weight requirements and available materials.
Consider what special features you want to incorporate into your custom welders table. Will your welders table include a grid of holes for fixturing? Do you need integrated storage drawers or shelves? Would casters make your welders table more functional in your space? Planning these elements before construction ensures your completed welders table meets all your requirements without costly modifications later.
DIY Welders Table Planning Checklist
- Determine dimensions based on your workspace and typical projects
Consider both the footprint and height of your welders table
- Select appropriate materials for your budget and requirements
Balance material cost with the durability needs of your welders table
- Plan for fixturing options on your welders table surface
Consider hole patterns, slots, or other clamping accommodations
- Design appropriate storage solutions into your welders table
Tool drawers, shelves, or holders for frequently used equipment
- Consider mobility requirements for your welders table
Fixed legs, leveling feet, or heavy-duty casters depending on needs
- Plan for proper grounding of your welders table
Include dedicated grounding points in your design
- Create detailed drawings or models of your welders table
Include measurements and material specifications
Construction Tips for DIY Welders Tables
Building a welders table is, appropriately, a welding project in itself—and one that requires careful attention to precision. Start by constructing the frame of your welders table, ensuring all corners are perfectly square and joints are strongly welded. Many DIY welders table builders use a combination of tack welds and measuring diagonals to verify squareness before completing the full welds on their welders table frame.
For the top surface of your welders table, flatness is crucial. If you're using a steel plate that isn't already machine-flattened, you may need to address warping issues. Some DIY welders table builders create a frame with cross-supports under the top plate, then use a series of carefully tightened bolts to pull the plate flat against this supporting structure. Others use careful welding techniques to minimize warping of their welders table top during attachment.
If you're incorporating a hole pattern into your welders table, ensure these holes are precisely positioned and perpendicular to the surface. Many builders create a drilling template to maintain consistency across their entire welders table surface. For more advanced fixturing systems, consider purchasing pre-made components that can be incorporated into your custom welders table design, combining DIY cost savings with professional-grade functionality.
Pro Tip for DIY Welders Table Builders
When building your own welders table, remember that the time spent ensuring precision during construction will pay dividends throughout the life of your welders table. A perfectly flat, square welders table makes every future welding project easier and more accurate. Take your time with the fundamental aspects of your welders table construction—you're building a workshop centerpiece that will serve you for years to come.
Optimizing Your Welders Table with Accessories
Whether you purchase a commercial welders table or build your own, accessories and add-ons can significantly enhance the functionality of your workstation. The right accessories transform a basic welders table into a comprehensive fabrication system that improves efficiency, precision, and versatility across diverse welding projects.
Clamping solutions are perhaps the most essential accessories for any welders table. These include C-clamps, toggle clamps, magnetic holders, and specialized fixturing clamps designed specifically for welders tables. For welders tables with hole patterns, dog-and-clamp systems provide versatile workholding options that can secure pieces in virtually any position on your welders table surface.
Positioning tools represent another valuable category of welders table accessories. These include adjustable angles, V-blocks, precision squares, and fixturing jigs that help maintain exact alignments during welding. Many professional welders invest in a set of positioning accessories that complement their welders table, allowing for repeatable setups and consistent results across similar projects.
Organization accessories keep your welders table workspace efficient and uncluttered. Tool holders, drawer systems, and specialized racks that attach to your welders table keep frequently used items within easy reach without consuming valuable working surface. Some welders tables include t-slots or mounting points specifically designed for attaching organizational accessories, creating a highly customized workflow around your welders table.
Conclusion: Investing in Quality for Long-Term Success
Whether you choose a professional manufactured welders table, a modular system, or a custom DIY solution, the quality of your welders table directly impacts the quality of your welding work. A well-designed welders table isn't merely a convenience—it's a fundamental tool that influences the precision, efficiency, and safety of every welding project you undertake.
When evaluating welders table options, consider long-term value rather than focusing solely on initial cost. A quality welders table represents a significant investment, but one that yields returns through improved work quality, reduced labor time, and enhanced capabilities. For professional welders, the right welders table is as essential to quality outcomes as their welding machine or personal skill.
The perfect welders table for your needs will depend on your specific work requirements, available space, mobility needs, and budget. By understanding the critical features of quality welders tables and carefully assessing your particular welding applications, you can select or build a welders table that will serve as the cornerstone of your workshop for years to come.
Looking for more welding equipment guides?
Explore our other articles on welding equipment, techniques, and best practices. Our comprehensive resources help both beginners and professionals make informed decisions about their welding setup and processes.

Michael Rivera
Michael is a certified welding instructor and fabrication specialist with over 20 years of experience in metal fabrication. He specializes in workshop setup and optimization, helping welders at all levels create efficient and productive work environments.