Published: November 25, 2025 • 8 min read
Types of Welders: The Definitive Guide to Welding Professionals and Processes
Understanding the distinct types of welders and welding processes to help you choose the right professional for your specific project needs
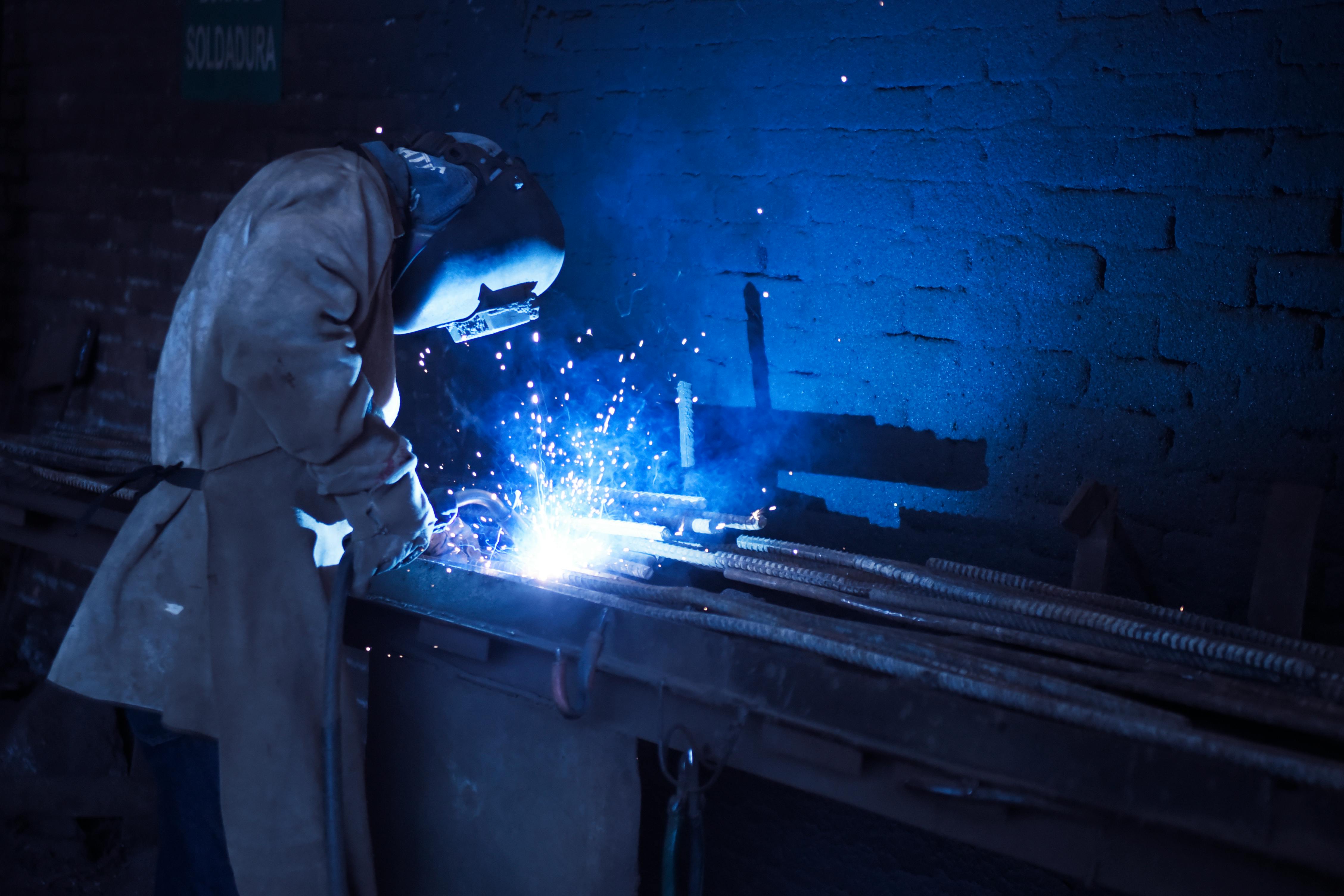
Understanding the Different Types of Welders
In the diverse world of metalworking, understanding the various types of welders is essential for both project success and career development. The term types of welders can refer to both the skilled professionals who perform welding operations and the equipment they use. This comprehensive guide explores all types of welders from both perspectives, providing valuable insights for hiring managers, project planners, and aspiring welding professionals alike. With advancements in technology and specialized applications continuing to evolve, the range of types of welders has expanded significantly in 2025.
The welding industry depends on different types of welders to address specific material challenges, environmental conditions, and project requirements. Whether you're looking to hire the right professional or considering a career path in welding, knowing the distinct types of welders and their specialties is crucial. From structural welders working on skyscrapers to underwater welders maintaining offshore platforms, each category of welding professional brings unique skills to the table. Similarly, the equipment types of welders use varies dramatically based on the application, from portable MIG machines to sophisticated laser welding systems.
Professional Types of Welders: Specializations and Skills
When discussing professional types of welders, we're referring to specialized tradespeople who have mastered specific welding processes and applications. The various types of welders are generally categorized by their primary welding method, industry focus, or working environment. Here's a comprehensive breakdown of the main professional types of welders you'll encounter in today's industry:
Structural Welders
These types of welders specialize in:
• Creating and repairing metal frameworks for buildings
• Working with heavy-gauge metals and structural beams
• Meeting strict code requirements for load-bearing structures
• Mastering vertical and overhead welding positions
• Interpreting complex blueprint specifications
• These types of welders often work in construction
Pipe Welders
Among the most skilled types of welders:
• Creating secure connections for fluid and gas transport
• Mastering techniques for cylindrical surfaces
• Working in multiple positions (6G certification)
• Meeting strict standards for pressure vessels
• Specializing in TIG, stick, or combination processes
• Highest-paid types of welders in many markets
Aerospace Welders
Precision-focused types of welders who:
• Work with exotic metals and alloys like titanium
• Maintain extremely tight tolerances and specifications
• Undergo rigorous certification and testing
• Primarily use TIG welding for precision control
• Create components that must withstand extreme conditions
• Represent some of the most specialized types of welders
Underwater Welders
These unique types of welders specialize in:
• Combining commercial diving with welding skills
• Performing wet welding directly in aquatic environments
• Working in hyperbaric chambers for dry welding
• Maintaining offshore structures and pipelines
• Operating in extremely hazardous conditions
• Earning premium wages among types of welders
Beyond these main categories, other specialized types of welders include military welders working on defense applications, automotive welders specializing in vehicle manufacturing and restoration, and artistic welders creating sculptures and ornamental pieces. The versatility of welding as a career is reflected in the numerous types of welders who have developed niche skills to meet specific market demands. Regardless of specialization, all types of welders require a fundamental understanding of metallurgy, safety protocols, and blueprint reading.
Equipment Types of Welders: Processes and Technologies
When discussing equipment types of welders, we're referring to the machines used to execute various welding processes. The market offers numerous types of welders designed for specific applications, materials, and skill levels. Understanding these different types of welders is crucial for selecting the right equipment for your projects. Let's examine the major types of welders available today:
MIG Welders (Metal Inert Gas)
MIG welders are among the most popular types of welders due to their versatility and ease of use. These types of welders feed a continuous wire electrode through a welding gun, creating an arc that melts the wire and base metals to form a joint. The process is shielded by an inert gas mixture that protects the weld from contamination.
Advantages of MIG types of welders:
- Easiest types of welders to learn for beginners
- High deposition rates compared to other types of welders
- Minimal slag and clean-up required
- Effective for thin to medium-thickness materials
- Available in various sizes for different applications
Popular MIG types of welders include:
• Entry-level: Hobart Handler 140, Lincoln Electric Easy MIG 140
• Mid-range: Miller Multimatic 215, ESAB Rebel 205ic
• Industrial: Miller Deltaweld 350, Lincoln Electric Power Wave S350
Price range for these types of welders: $500-$5,000+
TIG Welders (Tungsten Inert Gas)
Popular TIG types of welders include:
• Entry-level: AHP AlphaTIG 200X, Everlast PowerTIG 200DV
• Mid-range: Miller Syncrowave 210, Lincoln Electric Square Wave TIG 200
• Industrial: Miller Dynasty 300 DX, ESAB Heliarc 353i
Price range for these types of welders: $800-$8,000+
TIG welders represent precision-oriented types of welders that use a non-consumable tungsten electrode to produce the weld. The operator manually feeds a separate filler rod into the weld pool, allowing for exceptional control. These types of welders use inert gas shielding and are known for producing high-quality, clean welds.
Advantages of TIG types of welders:
- Highest precision control among all types of welders
- Excellent for thin materials and exotic metals
- Produces aesthetically pleasing welds
- No spatter and minimal clean-up
- Ideal for critical applications requiring highest quality
Stick Welders (SMAW)
Stick welders, also known as Shielded Metal Arc Welding (SMAW) types of welders, use a consumable electrode covered in flux to lay the weld. These types of welders are known for their simplicity, portability, and effectiveness in challenging conditions. Among all types of welders, stick machines are often considered the most versatile for outdoor and field work.
Advantages of Stick types of welders:
- Most portable of all types of welders
- Effective in windy or outdoor conditions
- Works on rusty or dirty materials
- Excellent for thick materials and structural applications
- Simple, reliable technology with fewer components to fail
- Among the most affordable types of welders
Popular Stick types of welders include:
• Entry-level: Lincoln Electric AC225, Forney 235
• Mid-range: Miller Thunderbolt 160, ESAB Miniarc Rogue
• Industrial: Miller XMT 350, Lincoln Electric Flextec 350X
Price range for these types of welders: $300-$3,000+
Multi-Process Welders
Multi-process types of welders have gained significant popularity in recent years. These versatile machines combine multiple welding processes in a single unit, typically offering MIG, TIG, and Stick capabilities. For workshops with diverse needs, these types of welders provide exceptional flexibility without requiring multiple machines.
Popular Multi-Process types of welders include:
• Entry-level: Eastwood MP200i, YesWelder MP200
• Mid-range: ESAB Rebel EMP 215ic, Lincoln Electric Power MIG 215
• Industrial: Miller Multimatic 300, Lincoln Electric Flextec 350X
Price range for these types of welders: $800-$6,000+
Advantages of Multi-Process types of welders:
- Most versatile of all types of welders
- Space-saving solution for small workshops
- Cost-effective compared to purchasing separate machines
- Ideal for users who work with various materials and projects
- Modern types of welders with advanced digital controls
- Excellent for learning different welding processes
Additional types of welders available in specialized applications include Flux-Cored Arc Welders (ideal for outdoor work and thicker materials), Plasma Arc Welders (for precision cutting and welding), and advanced robotic welding systems for automated manufacturing. Each of these types of welders offers distinct advantages for specific applications and material challenges.
Training and Certification for Different Types of Welders
Becoming proficient in various types of welders and welding processes requires proper training and certification. The path to becoming skilled in different types of welders typically involves a combination of formal education, hands-on training, and industry certifications. Let's explore the training requirements for different types of welders:
Educational Pathways for Different Types of Welders
Technical Schools
Offer focused programs for types of welders lasting 6-18 months. Students learn to operate multiple types of welders and develop fundamental skills.
Community Colleges
Provide associate degrees in welding technology, covering theory and practice with various types of welders. Often include business courses beneficial for career advancement.
Apprenticeships
On-the-job training with experienced types of welders, typically 3-4 years. Apprentices receive mentoring while working with different types of welders in real-world settings.
Certification Requirements for Professional Types of Welders
Certification is crucial for validating the skills of types of welders across various specializations. Different types of welders may require specific certifications based on their industry and application focus. The most recognized certifying bodies for types of welders include:
American Welding Society (AWS)
AWS offers the Certified Welder (CW) program, which tests types of welders on specific processes, positions, and materials. Their Certified Welding Inspector (CWI) credential is highly respected for those overseeing quality control. Advanced types of welders may pursue specialized certifications such as:
- Certified Welding Educator (CWE)
- Certified Radiographic Interpreter (CRI)
- Certified Welding Engineer (CWE)
- Certified Welding Supervisor (CWS)
Additional Certification Bodies for Types of Welders
- American Society of Mechanical Engineers (ASME) - Essential for types of welders working on pressure vessels and power systems
- American Petroleum Institute (API) - Critical for types of welders in oil and gas industries
- International Organization for Standardization (ISO) - Global standards relevant to all types of welders
- Occupational Safety and Health Administration (OSHA) - Safety certifications applicable to all types of welders
Career Outlook and Earnings for Different Types of Welders
The career prospects and earning potential vary significantly across different types of welders. Specialized types of welders with advanced certifications typically command higher salaries than general welders. Here's a breakdown of potential earnings and job outlook for various types of welders in 2025:
Types of Welders | Entry-Level Salary | Experienced Salary | Job Growth (5-year) |
---|---|---|---|
General Welders | $40,000 - $45,000 | $55,000 - $65,000 | 5% |
Pipe Welders | $52,000 - $60,000 | $75,000 - $95,000 | 8% |
Structural Welders | $45,000 - $50,000 | $60,000 - $75,000 | 6% |
Aerospace Welders | $55,000 - $65,000 | $85,000 - $110,000 | 10% |
Underwater Welders | $60,000 - $80,000 | $100,000 - $200,000 | 12% |
The demand for skilled types of welders remains strong across industries, particularly as infrastructure development and manufacturing continue to evolve. The most significant growth opportunities for types of welders are in:
High-Growth Industries for Types of Welders
- Renewable energy (wind turbine and solar panel manufacturing)
- Infrastructure revitalization (bridges, highways, water systems)
- Aerospace and defense
- Automated manufacturing
- Specialized fabrication for medical devices and technology
Emerging Opportunities for Types of Welders
- Robotic welding programming and supervision
- Additive manufacturing (3D printing with metals)
- Exotic materials welding (titanium, Inconel, specialized alloys)
- Welding inspection and quality assurance
- Welding education and training for new generations of welders
For those exploring careers as types of welders, the field offers significant advantages beyond just salary potential. Different types of welders enjoy job stability, opportunities for travel, clear advancement paths, and the satisfaction of creating tangible results. The diversity among types of welders means individuals can find specialized niches that match their interests and strengths.
Selection Guide: Choosing the Right Types of Welders for Your Needs
With numerous types of welders available on the market, selecting the right equipment for your specific needs can be challenging. This comprehensive selection guide will help you navigate the various types of welders to find the perfect match for your projects, skill level, and budget.
Key Considerations When Choosing Between Types of Welders
Material Types and Thickness
Different types of welders are optimized for specific metals and thicknesses. MIG welders handle thin sheet metal to medium plate, while stick welders excel with thicker materials.
Power Requirements
Consider your available power supply. Some types of welders require 220V power, while others can operate on standard 110V household current.
Skill Level
For beginners, MIG types of welders offer the easiest learning curve. TIG types of welders require more skill but deliver precision results. Stick welders have a moderate learning curve.
Portability Requirements
If mobility is important, consider the weight and size of different types of welders. Stick welders and some inverter-based types of welders offer excellent portability.
Budget Constraints
Types of welders vary significantly in price. Entry-level MIG and stick welders are more affordable, while TIG and multi-process types of welders represent larger investments.
Project Frequency
For occasional use, more affordable types of welders may suffice. For regular or professional use, invest in higher-duty cycle types of welders from reputable brands.
Recommendations Based on User Profiles
To simplify your selection process among various types of welders, we've created recommendations based on common user profiles. These suggestions will help you identify which types of welders are most suitable for specific situations:
Recommended types of welders:
- Entry-level MIG welder (110V)
- Flux core welder for outdoor projects
- Basic multi-process welder
Budget-friendly types of welders with straightforward operation make learning easier and allow for successful early projects.
Recommended types of welders:
- Mid-range multi-process welder
- Quality MIG welder with aluminum capability
- Portable stick welder for field work
Versatile, reliable types of welders that can handle diverse client needs while offering good value for the investment.
Recommended types of welders:
- Industrial-grade MIG welders
- High-end TIG welders with AC/DC capability
- Specialized types of welders for specific applications
Premium types of welders with high duty cycles, digital controls, and extensive warranty coverage provide long-term reliability for production environments.
Conclusion: The Future of Welding Technology and Professionals
As we've explored throughout this comprehensive guide, the diverse types of welders – both professionals and equipment – form the backbone of manufacturing, construction, and countless other industries. The evolution of welding continues at a rapid pace, with new types of welders emerging to meet specialized needs and technological advancements improving capabilities across the board.
For those considering a career in welding, understanding the various types of welders and their specializations provides a roadmap to potential career paths. The industry's diversity offers opportunities for everyone from creative artistic welders to highly technical aerospace specialists. Similarly, for those purchasing welding equipment, knowing the strengths and limitations of different types of welders ensures you select the right tool for your specific requirements.
As technology advances, we can expect even more specialized types of welders to emerge, with increased automation, improved user interfaces, and enhanced capabilities. However, regardless of these advancements, the fundamental principles that distinguish the various types of welders will remain relevant for years to come.
Use our interactive tool to find the perfect match among various types of welders based on your project requirements, budget, and experience level.
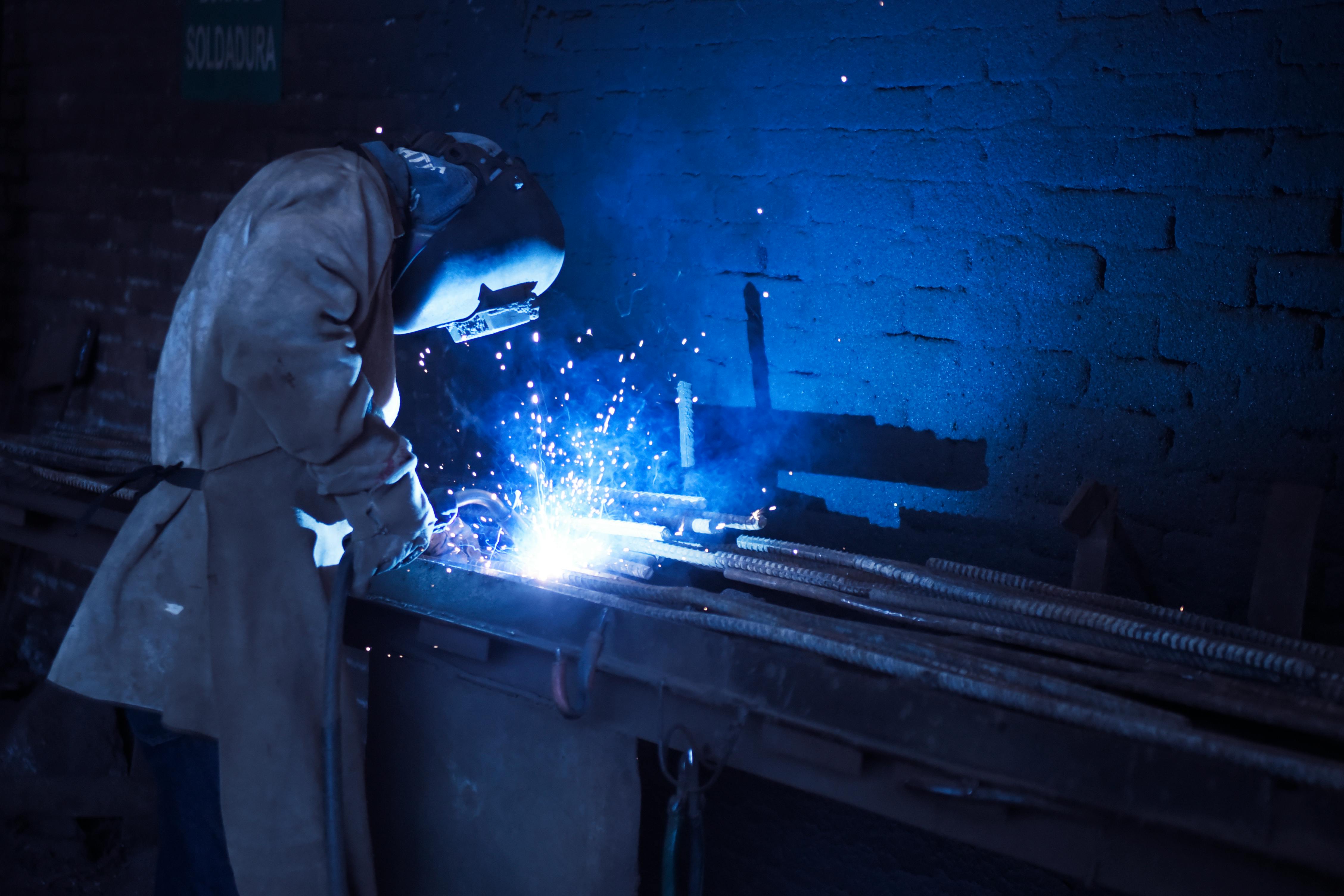
Jennifer Martinez
Jennifer is a certified welding instructor with over 15 years of experience teaching various types of welders. She specializes in helping beginners master different welding processes and has contributed to numerous industry publications on welding education.