发布日期: 2025年2月15日 • 阅读时间: 8分钟
TIG Welders for Aluminium: The Expert's Guide to Flawless Aluminum Welding
Comprehensive analysis of the best TIG welders for aluminium applications, with technical specifications and practical recommendations
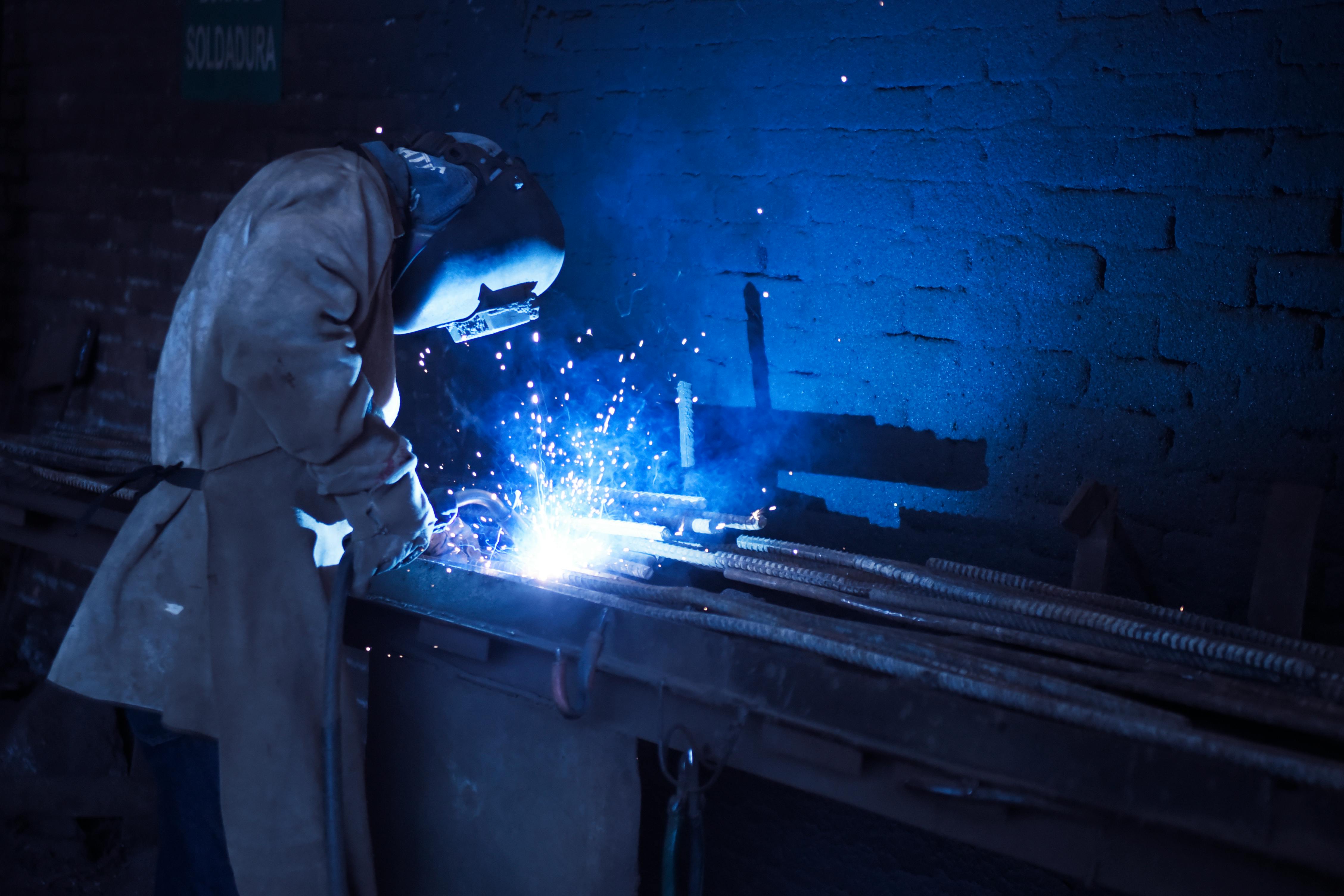
Understanding the Unique Requirements of TIG Welders for Aluminium
TIG welders for aluminium require specific features and capabilities not found in standard welding equipment. Aluminum's distinctive physical properties demand specialized TIG welders for aluminium with alternating current (AC) capability, proper shielding gas systems, and advanced power control features. This comprehensive guide explores the essential characteristics of TIG welders for aluminium, helping professionals and enthusiasts select the optimal equipment for their aluminum fabrication needs.
When working with aluminum, standard direct current (DC) welding processes prove inadequate, making purpose-designed TIG welders for aluminium essential. Unlike steel or stainless steel, aluminum forms a tenacious oxide layer that must be removed during the welding process. Only properly configured TIG welders for aluminium can effectively manage this challenge through the cleaning action provided by the alternating current's electrode positive phase. Understanding these fundamentals is crucial before investing in TIG welders for aluminium for your workshop or manufacturing facility.
Key Challenges When Using TIG Welders for Aluminium
Oxide Layer Removal
TIG welders for aluminium must effectively break down aluminum's natural oxide coating, which melts at 3,700°F compared to aluminum's 1,221°F melting point.
Heat Control
Superior TIG welders for aluminium provide precise amperage control to manage aluminum's high thermal conductivity, preventing distortion and burn-through.
AC Stability
Quality TIG welders for aluminium maintain stable arcs in AC mode, essential for consistent penetration and aesthetic bead appearance on aluminum projects.
The Science Behind TIG Welders for Aluminium
TIG welders for aluminium operate on principles significantly different from welding ferrous metals. Effective TIG welders for aluminium generate alternating current that switches between electrode negative (EN) and electrode positive (EP) polarity. During the EN phase, TIG welders for aluminium concentrate heat on the workpiece, creating penetration. In the EP phase, TIG welders for aluminium direct heat toward the tungsten electrode while simultaneously performing the crucial oxide-cleaning function that enables proper fusion of aluminum materials.
Advanced TIG welders for aluminium offer control over the AC frequency and balance settings. Higher frequencies from modern TIG welders for aluminium (typically 120-400Hz) create narrower, more focused arcs compared to the standard 60Hz produced by conventional TIG welders for aluminium. This capability allows welders to achieve greater precision, especially on thin aluminum sheets. AC balance control in specialized TIG welders for aluminium enables operators to adjust the ratio between cleaning and penetration phases, optimizing for specific aluminum alloys and joint configurations.
AC Waveform Options in Modern TIG Welders for Aluminium
Contemporary TIG welders for aluminium offer various AC waveform options:
• Sine Wave: Traditional waveform in basic TIG welders for aluminium
• Square Wave: Provides sharper transitions in premium TIG welders for aluminium
• Advanced Square Wave: Highest-end TIG welders for aluminium with optimized transitions
• Triangular Wave: Specialized TIG welders for aluminium for specific applications
• Soft Square Wave: Balanced performance in mid-range TIG welders for aluminium
Pulse Capabilities in TIG Welders for Aluminium
Pulsing functions in quality TIG welders for aluminium provide:
• Reduced heat input critical for aluminum welding
• Better control over the weld puddle with TIG welders for aluminium
• Decreased distortion in thin aluminum sections
• Improved penetration profile using specialized TIG welders for aluminium
• Superior cosmetic appearance of finished welds
• Ability to weld out-of-position with advanced TIG welders for aluminium
Essential Components of Professional TIG Welders for Aluminium
High-quality TIG welders for aluminium integrate several critical components that distinguish them from basic welding machines. When evaluating TIG welders for aluminium, professionals should carefully examine these elements to ensure optimal performance on aluminum projects:
Component | Function in TIG Welders for Aluminium | Importance for Aluminum Welding |
---|---|---|
AC/DC Power Source | Provides alternating current essential for TIG welders for aluminium applications | Critical - All effective TIG welders for aluminium must offer AC capability |
High-Frequency Start | Enables non-contact arc initiation in TIG welders for aluminium | Essential - Prevents tungsten contamination in aluminum welds |
AC Balance Control | Adjusts cleaning vs. penetration ratio in TIG welders for aluminium | Very Important - Optimizes performance of TIG welders for aluminium on different alloys |
AC Frequency Control | Modifies arc focus and stability in advanced TIG welders for aluminium | Important - Enhances precision of TIG welders for aluminium on thin materials |
Additionally, premium TIG welders for aluminium incorporate sophisticated cooling systems to manage the intense heat generated during aluminum welding operations. Water-cooled torches, frequently paired with high-end TIG welders for aluminium, allow for extended duty cycles and greater comfort during prolonged aluminum fabrication sessions. The torch design itself is specialized in quality TIG welders for aluminium, often featuring larger gas nozzles and tungsten electrodes specifically selected for their performance on aluminum alloys.
Leading Manufacturers of TIG Welders for Aluminium
The market for TIG welders for aluminium features several prominent manufacturers, each offering distinctive approaches to aluminum welding challenges. These established brands have developed specialized TIG welders for aluminium that incorporate proprietary technologies addressing the unique requirements of aluminum fabrication. Understanding the strengths of each manufacturer's TIG welders for aluminium can help professionals select equipment that aligns with their specific needs.
Miller Electric TIG Welders for Aluminium
Miller's TIG welders for aluminium are renowned for:
• The Syncrowave® series - specialized TIG welders for aluminium with advanced AC features
• Dynasty® models offering superior TIG welders for aluminium performance with adjustable AC frequency (20-400Hz)
• Auto-Line™ technology for consistent performance in their TIG welders for aluminium
• Blue Lightning™ high-frequency arc starting in premium TIG welders for aluminium
• Pro-Set™ technology simplifying setup of TIG welders for aluminium applications
• Exceptional resale value among TIG welders for aluminium
Lincoln Electric TIG Welders for Aluminium
Lincoln Electric offers advanced TIG welders for aluminium featuring:
• Square Wave® series - dedicated TIG welders for aluminium with intuitive interfaces
• Precision TIG® models with exclusive Micro-Start™ technology for TIG welders for aluminium
• Advanced Waveform Control in their TIG welders for aluminium
• AC Auto-Balance® optimizing TIG welders for aluminium performance
• Enhanced aluminum puddle control in high-end TIG welders for aluminium
• Rugged durability in field-use TIG welders for aluminium
ESAB TIG Welders for Aluminium
ESAB's TIG welders for aluminium stand out with:
• The Rebel™ series offering portable yet capable TIG welders for aluminium
• Heliarc® technology in their professional TIG welders for aluminium
• QWave™ technology enhancing arc stability in TIG welders for aluminium
• Comprehensive frequency and balance adjustment in premium TIG welders for aluminium
• PFC (Power Factor Correction) for efficient TIG welders for aluminium
• Global service network supporting their TIG welders for aluminium
Fronius TIG Welders for Aluminium
Fronius delivers innovative TIG welders for aluminium with:
• TransTig and MagicWave series - specialized TIG welders for aluminium
• Active Wave® technology in their premium TIG welders for aluminium
• Digital signal processors enhancing TIG welders for aluminium performance
• Automatic cap-shaping function on advanced TIG welders for aluminium
• RPI ignition improving arc starts in TIG welders for aluminium applications
• European engineering excellence in TIG welders for aluminium
Comparing Key Features Among Top TIG Welders for Aluminium
When evaluating premium TIG welders for aluminium, several technical specifications differentiate models and directly impact their aluminum welding capabilities. The following comparison highlights the most critical features found in professional-grade TIG welders for aluminium, providing perspective on how these specifications influence performance on aluminum projects:
Technical Specifications of Leading TIG Welders for Aluminium
AC Frequency Range
Professional <strong>TIG welders for aluminium</strong> typically offer adjustable AC frequency from 20-400Hz. Higher-end <strong>TIG welders for aluminium</strong> may extend to 500Hz or beyond, allowing exceptionally precise arc focus for aluminum fabrication. Budget <strong>TIG welders for aluminium</strong> often limit frequency to 60Hz or a narrower range.
AC Balance Control
Quality <strong>TIG welders for aluminium</strong> provide balance control from approximately 60% EN/40% EP to 30% EN/70% EP. Advanced <strong>TIG welders for aluminium</strong> offer finer incremental adjustments, while basic <strong>TIG welders for aluminium</strong> may offer limited preset options or fixed balance settings.
Amperage Range and Stability
Industrial <strong>TIG welders for aluminium</strong> provide amperage ranges from approximately 5-350A with ±3% stability. Premium <strong>TIG welders for aluminium</strong> may offer precision control down to 1A with ±1% stability, while entry-level <strong>TIG welders for aluminium</strong> typically start at 10-15A with less refined stability.
Pulse Capabilities
High-end <strong>TIG welders for aluminium</strong> offer pulse frequencies from 0.1-500Hz or higher, with independent control of peak/background current and duration. Mid-range <strong>TIG welders for aluminium</strong> typically provide 0.5-200Hz with preset ratios, while basic <strong>TIG welders for aluminium</strong> might offer limited pulsing options or none at all.
Price Tiers of TIG Welders for Aluminium
TIG welders for aluminium are available across a wide range of price points, with distinct feature sets and capabilities at each level. Understanding the typical offerings and limitations of TIG welders for aluminium in different price brackets helps buyers make informed decisions that balance budget constraints with aluminum welding requirements:
Price Category | Typical Features in TIG Welders for Aluminium | Suitable Applications |
---|---|---|
Entry-Level ($800-$1,500) | Basic AC/DC capability in budget TIG welders for aluminium; limited control options; typically 15-200A range; fixed AC frequency in most affordable TIG welders for aluminium | Hobbyist aluminum projects; thin material repairs; light-duty aluminum fabrication with basic TIG welders for aluminium |
Mid-Range ($1,500-$3,500) | Enhanced control features in these TIG welders for aluminium; adjustable AC frequency (typically 20-150Hz); improved duty cycles; basic pulse options in mid-tier TIG welders for aluminium | Professional maintenance shops; small fabrication businesses; more frequent aluminum welding with versatile TIG welders for aluminium |
Professional ($3,500-$7,000) | Comprehensive control systems in professional TIG welders for aluminium; expanded AC frequency range (20-400Hz); advanced waveform options; high-performance cooling in premium TIG welders for aluminium | Professional aluminum fabrication; aerospace components; critical structural welding requiring superior TIG welders for aluminium |
Industrial ($7,000+) | Maximum precision and control in industrial TIG welders for aluminium; complete programmability; highest duty cycles; water cooling standard; advanced memory functions in high-end TIG welders for aluminium | Production environments; automated systems; aerospace and critical applications demanding the best TIG welders for aluminium |
Selecting the Ideal TIG Welders for Aluminium: A Comprehensive Buying Guide
Choosing the optimal TIG welders for aluminium requires careful consideration of several factors beyond basic price comparisons. This comprehensive buying guide helps professionals navigate the complex landscape of TIG welders for aluminium, ensuring their investment aligns with specific aluminum fabrication requirements. By methodically evaluating these key aspects of TIG welders for aluminium, buyers can make informed decisions that enhance productivity and weld quality.
Critical Selection Criteria for TIG Welders for Aluminium
Material Thickness Range
Consider your typical aluminum projects:
• Thin sheet (0.5-3mm): Entry to mid-range TIG welders for aluminium with good low-amp stability
• Medium plate (3-6mm): Mid-range TIG welders for aluminium with 200A+ capacity
• Heavy plate (6mm+): Professional TIG welders for aluminium with 250A+ output
• Mixed thicknesses: Versatile TIG welders for aluminium with wide amperage range
Control Sophistication
Match controls to operator expertise:
• Beginners: TIG welders for aluminium with preset programs
• Intermediate: TIG welders for aluminium with essential adjustments
• Advanced: TIG welders for aluminium with comprehensive customization
• Production: TIG welders for aluminium with programmable memory
Duty Cycle Requirements
Factor in your production volume:
• Occasional use: Basic TIG welders for aluminium with standard duty cycles
• Regular projects: Mid-tier TIG welders for aluminium with 40-60% duty cycle
• Production work: Professional TIG welders for aluminium with 80-100% duty cycle
• Critical applications: Industrial water-cooled TIG welders for aluminium
Secondary Considerations for TIG Welders for Aluminium
Beyond the primary selection criteria, several additional factors should influence the choice of TIG welders for aluminium. These secondary considerations can significantly impact the long-term satisfaction and productivity achieved with TIG welders for aluminium:
Input Power and Installation Requirements
- Ensure your facility can support the input requirements of selected <strong>TIG welders for aluminium</strong> (single-phase 230V vs. three-phase 460V)
- Consider multi-voltage <strong>TIG welders for aluminium</strong> if portability between different sites is necessary
- Factor in installation costs for higher-end <strong>TIG welders for aluminium</strong> requiring dedicated electrical service
- Verify generator compatibility for field use of portable <strong>TIG welders for aluminium</strong>
Torch Options and Consumables
- Evaluate included torch quality with <strong>TIG welders for aluminium</strong> - many require upgrades for serious aluminum work
- Consider water-cooled options for intensive aluminum work with professional <strong>TIG welders for aluminium</strong>
- Factor in cost and availability of consumables for specific <strong>TIG welders for aluminium</strong> models
- Consider ergonomics for extended aluminum welding sessions with <strong>TIG welders for aluminium</strong>
Top Applications for Specialized TIG Welders for Aluminium
TIG welders for aluminium excel in numerous applications where precision, aesthetics, and structural integrity are paramount. The following sectors represent the primary industries where specialized TIG welders for aluminium demonstrate their full potential:
Aerospace and Aviation
Advanced TIG welders for aluminium are essential in aerospace applications:
• Aircraft structural components require premium TIG welders for aluminium
• Fuel systems welded with specialized TIG welders for aluminium
• Satellite and space vehicle components fabricated using high-end TIG welders for aluminium
• Aviation repair operations utilizing portable TIG welders for aluminium
• Precision components demanding superior TIG welders for aluminium with maximum control
• Critical safety applications requiring certified TIG welders for aluminium equipment
Automotive and Transportation
TIG welders for aluminium play crucial roles in modern transportation:
• Lightweight vehicle frame construction using specialized TIG welders for aluminium
• Performance racing components fabricated with high-end TIG welders for aluminium
• Custom motorcycle frames crafted using precision TIG welders for aluminium
• Aluminum body panel repairs with portable TIG welders for aluminium
• Fuel cell systems requiring contamination-free TIG welders for aluminium
• Electric vehicle battery enclosures welded with specialized TIG welders for aluminium
Marine and Shipbuilding
TIG welders for aluminium enable critical marine fabrication:
• Aluminum boat hull construction with industrial TIG welders for aluminium
• Corrosion-resistant components created using specialized TIG welders for aluminium
• Marine hardware installation with portable TIG welders for aluminium
• Custom yacht fittings fabricated with premium TIG welders for aluminium
• Offshore equipment repair using rugged TIG welders for aluminium
• Fuel and water tank production with certified TIG welders for aluminium
Food and Beverage Equipment
TIG welders for aluminium ensure sanitary fabrication:
• Brewing and distilling equipment built with specialized TIG welders for aluminium
• Dairy processing components created using sanitary TIG welders for aluminium
• Food conveyance systems assembled with precision TIG welders for aluminium
• Pharmaceutical equipment fabricated using certified TIG welders for aluminium
• Sanitary tubing connections made with dedicated TIG welders for aluminium
• Custom food processing machinery built with industrial TIG welders for aluminium
Expert Tips for Maximizing Performance with TIG Welders for Aluminium
Even the most advanced TIG welders for aluminium require proper setup and technique to achieve optimal results. Professional welders with extensive experience using TIG welders for aluminium recommend the following practices to maximize performance and weld quality:
Professional Techniques for TIG Welders for Aluminium
Proper Equipment Setup
Configure your <strong>TIG welders for aluminium</strong> with 2-3 cfh higher flow rates than you would use for steel. For advanced <strong>TIG welders for aluminium</strong>, start with an AC balance of approximately 70% EN / 30% EP and adjust based on results. In premium <strong>TIG welders for aluminium</strong> with frequency control, begin at 100-120Hz for general aluminum work.
Material Preparation
Even with excellent <strong>TIG welders for aluminium</strong>, proper material preparation remains essential. Dedicate a stainless steel brush exclusively for aluminum preparation when using <strong>TIG welders for aluminium</strong>. Clean with acetone rather than brake cleaner, which can leave residues that compromise weld quality from <strong>TIG welders for aluminium</strong>.
Electrode Selection
For optimal results with <strong>TIG welders for aluminium</strong>, use pure tungsten (green) or zirconiated tungsten (brown) electrodes rather than thoriated options. Professional users of <strong>TIG welders for aluminium</strong> recommend ball-shaped electrode tips for aluminum, unlike the pointed tips used with <strong>TIG welders for aluminium</strong> in DC mode on steel.
Advanced Techniques
Experienced operators of <strong>TIG welders for aluminium</strong> often employ pulse functions to reduce heat input and minimize distortion. For thin materials, experts using <strong>TIG welders for aluminium</strong> recommend higher frequencies (200-500Hz) to create a focused arc that prevents burn-through while maintaining penetration.
Conclusion: Investing in Quality TIG Welders for Aluminium
The selection of appropriate TIG welders for aluminium represents a critical decision for professionals and businesses engaged in aluminum fabrication. Quality TIG welders for aluminium provide the specialized features necessary to overcome the unique challenges presented by this versatile but demanding material. While premium TIG welders for aluminium require significant investment, the enhanced productivity, superior weld quality, and expanded capabilities justify the expenditure for serious aluminum welding operations.
As aluminum continues to gain prominence in industries prioritizing lightweight, corrosion-resistant materials, the demand for capable TIG welders for aluminium will only increase. By understanding the technical requirements and operational considerations of TIG welders for aluminium, welding professionals can make informed equipment selections that enhance their competitive advantage. Whether for aerospace components, custom automotive fabrication, or architectural applications, specialized TIG welders for aluminium remain the gold standard for achieving exceptional results on aluminum materials.
Remember that even the most advanced TIG welders for aluminium require skilled operators to achieve their full potential. Investing in both quality equipment and proper training ensures that your TIG welders for aluminium deliver maximum return on investment through superior productivity, reduced rework, and enhanced finished product quality. With the right combination of equipment, knowledge, and technique, TIG welders for aluminium enable fabrication professionals to transform this challenging metal into precisely crafted, aesthetically pleasing, and structurally sound components.
Our team of welding experts can provide tailored recommendations for TIG welders for aluminium based on your specific application requirements, production volume, and budget considerations.
Frequently Asked Questions About TIG Welders for Aluminium
Can standard DC TIG welders be used for aluminum?
No, standard DC-only TIG welders for aluminium cannot effectively weld aluminum. Proper TIG welders for aluminium must have AC capability to remove the oxide layer that forms on aluminum. Without the cleaning action provided by the EP portion of the AC cycle in TIG welders for aluminium, the oxide layer would prevent proper fusion, resulting in poor-quality welds with inclusions and lack of penetration. All effective TIG welders for aluminium must offer AC output.
What size TIG welder do I need for aluminum?
The required size of TIG welders for aluminium depends primarily on material thickness. For aluminum up to 1/8" (3.2mm), TIG welders for aluminium with 150-180A capacity are sufficient. For material 1/8" to 1/4" (3.2-6.4mm), TIG welders for aluminium in the 200-250A range are recommended. Heavier materials exceeding 1/4" require industrial TIG welders for aluminium with 300A+ capability. Remember that aluminum requires approximately 30% more amperage than similarly thick steel when selecting TIG welders for aluminium.
Are water-cooled torches necessary for TIG welders for aluminium?
Water-cooled torches are not strictly necessary for all TIG welders for aluminium applications but become increasingly important as amperage and duty cycle requirements increase. For occasional aluminum welding below 150A with TIG welders for aluminium, air-cooled torches may suffice. However, professional applications of TIG welders for aluminium typically benefit from water-cooled systems, which allow for extended welding periods, improve operator comfort, and enhance the longevity of consumables in TIG welders for aluminium used intensively.
How do I prevent contamination when using TIG welders for aluminium?
Preventing contamination when using TIG welders for aluminium requires several precautions. First, dedicate specific equipment (grinding wheels, wire brushes, etc.) exclusively for aluminum preparation when using TIG welders for aluminium. Second, thoroughly clean materials with appropriate solvents before welding with TIG welders for aluminium. Third, use pure argon shielding gas with TIG welders for aluminium rather than mixed gases. Finally, ensure proper storage of filler materials used with TIG welders for aluminium to prevent contamination from shop environments.
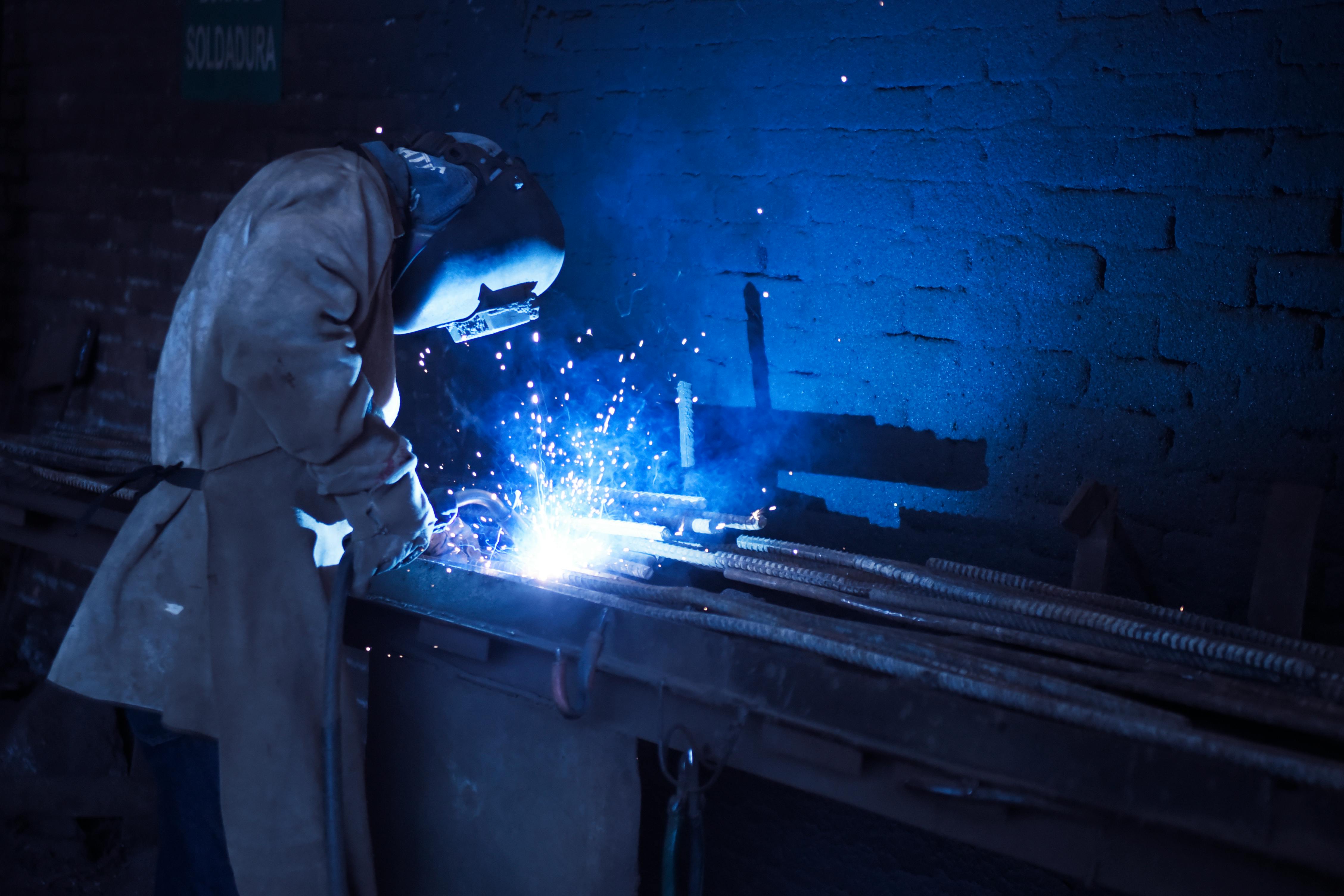
David Chen
David is a certified welding instructor and aluminum fabrication specialist with over 18 years of experience in aerospace and high-performance automotive applications. He has trained hundreds of welders in advanced TIG techniques for aluminum and regularly consults on equipment selection for manufacturing facilities.