Published: May 28, 2025 • Reading time: 8 minutes
Stick Welders: The Ultimate Guide to Shielded Metal Arc Welding
Discover everything you need to know about stick welders, from selecting the right machine to mastering essential techniques
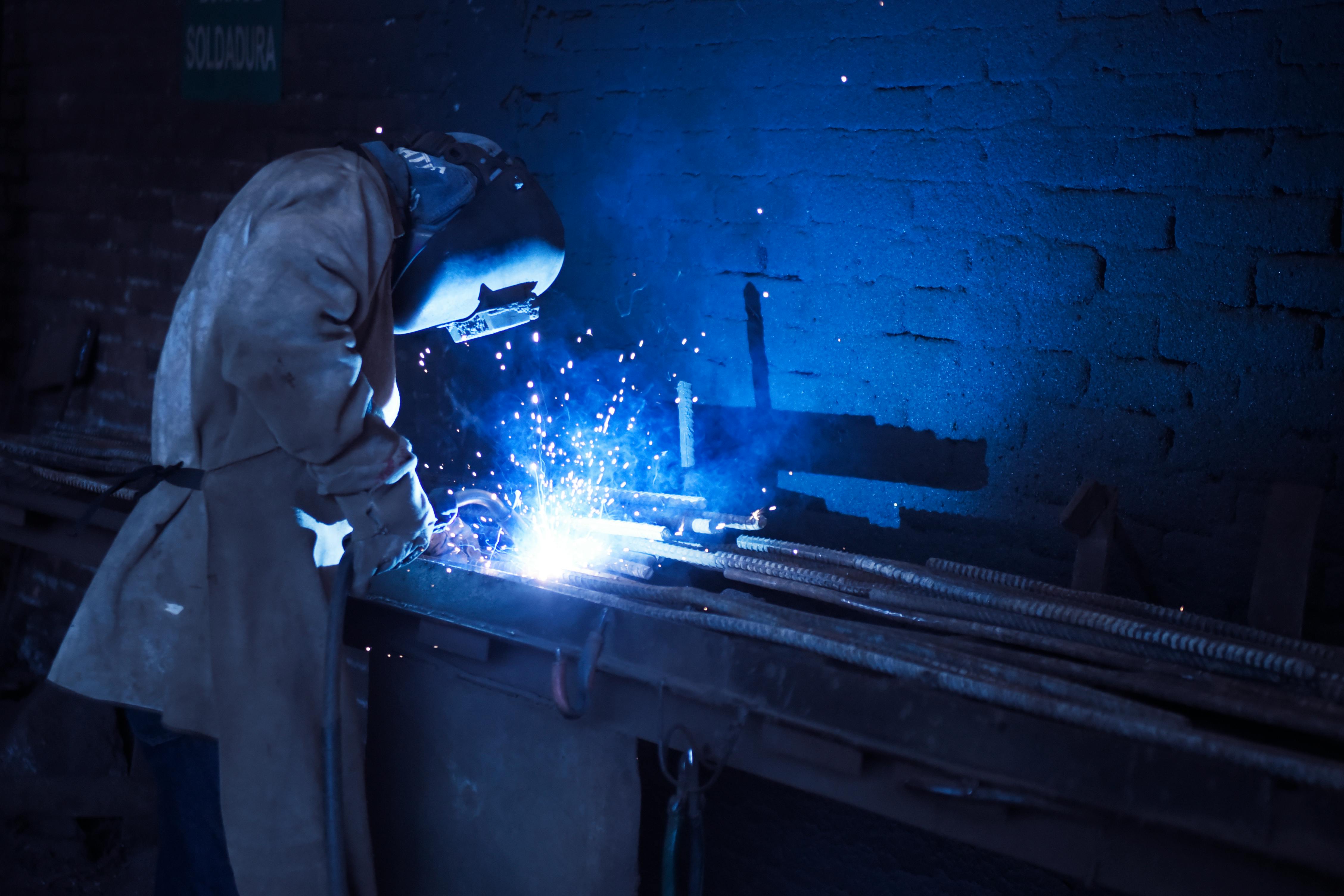
Understanding Stick Welders: The Foundation of Arc Welding
Stick welders, also known as Shielded Metal Arc Welding (SMAW) machines, represent one of the most versatile and widely used welding processes in the industry. When you're looking for reliable stick welders for your projects, understanding the fundamentals is essential. Stick welders operate by creating an electric arc between the electrode and the workpiece, melting both the electrode and the base material to form a strong bond.
The popularity of stick welders stems from their remarkable versatility and portability. Unlike other welding methods, stick welders can function effectively in challenging environments, including outdoor settings with wind or rain, and on dirty or rusty materials. This makes stick welders the preferred choice for construction sites, field repairs, and maintenance tasks where conditions are less than ideal.
Key Advantages of Stick Welders
Versatility
Stick welders can work with a wide variety of metals, including steel, stainless steel, cast iron, and many alloys. This versatility makes stick welders essential tools in many workshops and industrial settings.
Portability
Modern stick welders are designed with portability in mind. Many models of stick welders are lightweight and compact, making them easy to transport to different job sites or move around your workshop.
Reliability
Stick welders have fewer components than other welding systems, resulting in greater reliability and lower maintenance requirements. The simplicity of stick welders makes them durable tools that can withstand harsh working conditions.
How Stick Welders Work: The Science Behind the Arc
To fully appreciate stick welders, it's important to understand the science behind them. Stick welders create an electric arc between the electrode and the workpiece, generating intense heat (up to 10,000°F) that melts both the electrode and the base metal. The coating on the electrode of stick welders creates a shielding gas that protects the weld pool from atmospheric contamination.
The electrodes used with stick welders are classified by their coating type and intended application. When using stick welders, you'll encounter electrodes like the popular 6010, 6011, 6013, and 7018, each designed for specific welding situations. The electrode selection is critical when working with stick welders as it determines the weld's characteristics, including penetration, strength, and appearance.
One of the most significant advantages of stick welders is their ability to operate with both AC (alternating current) and DC (direct current) power. Modern stick welders often provide both options, with DC generally offering better arc stability and weld quality. When purchasing stick welders, considering whether you need AC, DC, or both capabilities is essential based on the materials you'll be welding.
Selecting the Right Stick Welder for Your Needs
When investing in stick welders, several key factors should guide your decision. Not all stick welders are created equal, and finding the right match for your specific requirements will ensure optimal performance and value for your investment.
Power Requirements and Output
Stick welders come in various power configurations, from 110V models suitable for home use to 220V and 480V industrial stick welders. The power output of stick welders is measured in amps, with entry-level stick welders typically offering 100-140 amps, while professional-grade stick welders can deliver up to 300 amps or more.
When choosing among available stick welders, consider the thickness of the materials you'll be welding. As a general rule, you need approximately 1 amp for every 0.001 inch of material thickness. Therefore, if you're welding 1/4 inch steel (0.25 inches), your stick welders should provide at least 250 amps of power for optimal results.
Duty Cycle Considerations
The duty cycle is a critical specification for stick welders that indicates how long the machine can operate continuously before requiring a cooling period. For example, a stick welder with a 30% duty cycle at 200 amps can run for 3 minutes out of a 10-minute period at that amperage before needing to cool down.
Professional-grade stick welders typically offer higher duty cycles, with some industrial stick welders providing 60% or even 100% duty cycles at specific amperage settings. When evaluating stick welders, consider your typical welding duration to ensure the machine can handle your workload without frequent interruptions.
Portability Factors
If you need to transport your equipment frequently, consider the weight and design of stick welders. Modern inverter-based stick welders are significantly lighter than traditional transformer-based units, with some portable stick welders weighing less than 20 pounds while still delivering impressive performance.
- Inverter technology has revolutionized the portability of stick welders
- Look for stick welders with carrying handles or shoulder straps for easy transport
- Consider battery-powered stick welders for extreme portability in remote locations
Additional Features
Modern stick welders often come with advanced features that enhance performance and ease of use. When comparing stick welders, look for these valuable additions:
- Hot start technology improves arc starting, especially valuable in entry-level stick welders
- Anti-stick function prevents electrodes from sticking to the workpiece, a common issue with stick welders
- Arc force control helps maintain a stable arc when working with stick welders in challenging positions
- Dual voltage capability allows stick welders to operate on both 110V and 220V power supplies
Type of Stick Welder | Typical Price Range | Best Applications |
---|---|---|
Entry-Level Stick Welders | $100 - $300 | DIY projects, light repairs, and hobbyist applications where stick welders are used occasionally |
Mid-Range Stick Welders | $300 - $700 | Small workshops, farms, and moderate fabrication where stick welders are used regularly but not continuously |
Professional Stick Welders | $700 - $1,500 | Professional fabrication shops and contractors requiring reliable stick welders for daily use |
Industrial Stick Welders | $1,500+ | Industrial manufacturing, construction sites, and environments where stick welders are used continuously under demanding conditions |
Leading Brands and Models of Stick Welders
The market offers numerous stick welders from reputable manufacturers. Understanding the strengths of major brands can help you identify the most suitable stick welders for your specific needs. Here's an overview of leading stick welders and what they offer:
Lincoln Electric Stick Welders
Lincoln Electric offers some of the most respected stick welders in the industry, known for their durability and performance. Their Tombstone series of stick welders has been a staple in workshops for decades, while their advanced inverter-based stick welders like the Power Arc series represent cutting-edge technology.
Notable features of Lincoln Electric stick welders include:
- Exceptional build quality and durability, making their stick welders long-term investments
- Advanced arc control in higher-end stick welders for superior weld quality
- Excellent technical support and warranty coverage for their stick welders
Miller Electric Stick Welders
Miller Electric produces premium stick welders renowned for their innovation and reliability. Their Thunderbolt and Maxstar series of stick welders offer exceptional performance for professionals and serious hobbyists. Miller stick welders are particularly praised for their arc stability and ease of use.
Key advantages of Miller stick welders include:
- Industry-leading arc performance in their stick welders, making them easier to use
- Multi-process capabilities in many stick welders, offering TIG and other processes
- Superior energy efficiency in their inverter-based stick welders
ESAB Stick Welders
ESAB offers a comprehensive range of stick welders known for their exceptional value and performance. From the affordable Rogue series to the professional-grade Rebel stick welders, ESAB provides reliable options for every level of user. ESAB stick welders often feature innovative technologies at competitive price points.
ESAB stick welders stand out for their:
- Excellent value proposition, with feature-rich stick welders at competitive prices
- User-friendly interfaces on their stick welders, even in advanced models
- Robust construction suited for demanding environments where stick welders must perform reliably
Budget-Friendly Stick Welders
For hobbyists and occasional users, brands like Forney, Hobart, and YesWelder offer affordable stick welders that deliver impressive performance for their price point. These budget-friendly stick welders have made welding more accessible to DIY enthusiasts and those just starting in the trade.
Considerations when evaluating budget stick welders:
- Focus on duty cycle, as less expensive stick welders often have limited continuous operation time
- Check for essential features like hot start and anti-stick, which improve usability in entry-level stick welders
- Research warranty terms, as support for budget stick welders varies widely between manufacturers
Mastering Stick Welding Techniques
Even the most advanced stick welders require proper technique to produce quality welds. Whether you're new to stick welders or looking to refine your skills, these fundamental techniques will help you achieve better results with your stick welders.
Essential Stick Welding Techniques
Proper Arc Starting
When using stick welders, start the arc by either scratching the electrode across the workpiece like a match or using a tapping motion. Modern stick welders with hot start features make this process easier, but proper technique remains essential. Practice controlling the arc length with your stick welders to maintain consistent heat input.
Electrode Angle and Movement
With stick welders, maintain a 20-30 degree angle in the direction of travel for most applications. When using stick welders for vertical welds, a slight side-to-side weaving motion helps create wider beads. The travel speed with stick welders should be adjusted based on the puddle formation and desired bead appearance.
Managing the Slag
One unique aspect of stick welders is the formation of slag that covers and protects the weld. After completing a pass with stick welders, allow the weld to cool slightly before removing the slag with a chipping hammer and wire brush. Always remove all slag before adding additional passes when using stick welders for multi-pass welds.
Common Applications for Stick Welders
Stick welders excel in various applications due to their versatility and adaptability. Understanding where stick welders perform best will help you maximize the value of your equipment and achieve optimal results in different scenarios.
Construction and Structural Welding
Stick welders are the preferred choice for structural steel welding in construction. The ability of stick welders to operate in windy conditions and on less-than-clean surfaces makes them ideal for construction sites. When using stick welders for structural applications, E7018 electrodes are commonly employed for their high strength and low hydrogen characteristics.
For structural applications, higher-amperage stick welders (200+ amps) are typically required to ensure proper penetration in thicker materials. The durability of stick welders also makes them well-suited for the demanding environments found on construction sites.
Repair and Maintenance
For maintenance and repair tasks, stick welders offer unmatched versatility. Whether fixing agricultural equipment, performing auto body repairs, or maintaining industrial machinery, stick welders can handle a wide range of materials and thicknesses. The portability of modern stick welders makes them perfect for field repairs where mobility is essential.
When using stick welders for repair work, having a range of electrodes available allows you to adapt to different materials. For instance, stick welders with E6013 electrodes are excellent for sheet metal repairs, while stick welders with E7014 electrodes work well for filling larger gaps.
Pipeline and Pressure Vessel Welding
High-end stick welders are extensively used in pipeline construction and pressure vessel fabrication. These critical applications require the consistent penetration and strength that quality stick welders can provide. Pipeline welders often prefer stick welders with DC output for better arc control when working on the root passes of pipe joints.
Professional-grade stick welders with precise amperage control are essential for code-compliant pipeline work. Many pipeline contractors use engine-driven stick welders that provide both welding power and auxiliary power in remote locations where pipelines are often constructed.
Artistic and Ornamental Welding
Stick welders are increasingly popular for artistic and ornamental metal work. The distinctive appearance of stick welds, which can be emphasized or refined depending on technique, offers artists unique aesthetic possibilities. Stick welders allow artists to work with various metals and create textures that other welding processes cannot achieve as easily.
For artistic applications, smaller stick welders with precise amperage control at the lower end of the spectrum (20-90 amps) are ideal. Artists using stick welders often experiment with different electrode types to achieve various visual effects in their metalwork creations.
Maintaining Your Stick Welder
Proper maintenance extends the life of stick welders and ensures consistent performance. While stick welders are generally robust, following these maintenance practices will keep your equipment in optimal condition:
- Regularly clean the interior of your stick welder with compressed air to remove dust and debris
Dust accumulation is a common cause of component failure in stick welders, particularly in inverter models
- Inspect and tighten electrical connections periodically
Loose connections can cause performance issues and potentially damage your stick welder
- Check and replace worn welding cables and electrode holders
Damaged cables can affect welding performance and pose safety risks when using stick welders
- Keep your stick welder in a dry environment when not in use
Although stick welders can operate in damp conditions, storing them in a dry place prevents internal corrosion
- Follow the manufacturer's recommended maintenance schedule
Professional-grade stick welders often have specific maintenance requirements detailed in the owner's manual
Frequently Asked Questions About Stick Welders
Are stick welders suitable for beginners?
Yes, stick welders can be excellent for beginners, although they do have a steeper learning curve than some other welding processes. Entry-level stick welders are affordable and versatile, making them good starter machines. Features like hot start and anti-stick in modern stick welders make the learning process easier. Many welding professionals recommend starting with stick welders because the skills developed transfer well to other welding processes.
Can stick welders weld aluminum?
While stick welders are not the ideal choice for aluminum, they can weld aluminum with special electrodes. When using stick welders for aluminum, you'll need specific aluminum electrodes (such as E4043) and typically require AC output stick welders. The results with stick welders on aluminum generally won't match the quality of TIG or MIG welding on this material, but stick welders can handle aluminum in situations where other equipment isn't available.
What's the difference between AC and DC stick welders?
Stick welders with DC (Direct Current) output generally provide more stable arcs and better weld quality, especially for detailed work. Stick welders with AC (Alternating Current) output are typically less expensive and can be advantageous for certain applications like welding cast iron or using electrodes that perform better with AC. Many professional stick welders offer both AC and DC capabilities, allowing welders to select the best current type for their specific application.
How do inverter stick welders compare to transformer-based models?
Inverter stick welders use advanced electronics to convert power more efficiently, resulting in machines that are smaller, lighter, and often more feature-rich than traditional transformer stick welders. While transformer stick welders are generally more durable and simpler to repair, inverter stick welders offer better arc control, are more energy-efficient, and provide features like hot start, anti-stick, and arc force control. For portable applications, inverter stick welders have largely replaced transformer models due to their significant weight advantage.
Conclusion: Investing in the Right Stick Welder
Stick welders remain an essential tool for professionals and hobbyists alike due to their versatility, reliability, and effectiveness across diverse applications. When selecting stick welders, carefully consider your specific requirements, including the materials you'll be welding, your working environment, and your budget constraints.
As technology advances, stick welders continue to evolve with enhanced features and improved performance. Whether you choose budget-friendly entry-level stick welders or invest in professional-grade equipment, understanding the capabilities and limitations of your machine will help you achieve optimal results in your welding projects.
For beginners, stick welders offer an excellent introduction to welding fundamentals that build a strong technical foundation. For professionals, high-quality stick welders provide the reliability and performance needed for demanding applications. With proper technique and regular maintenance, your stick welders will serve as dependable tools for years to come.
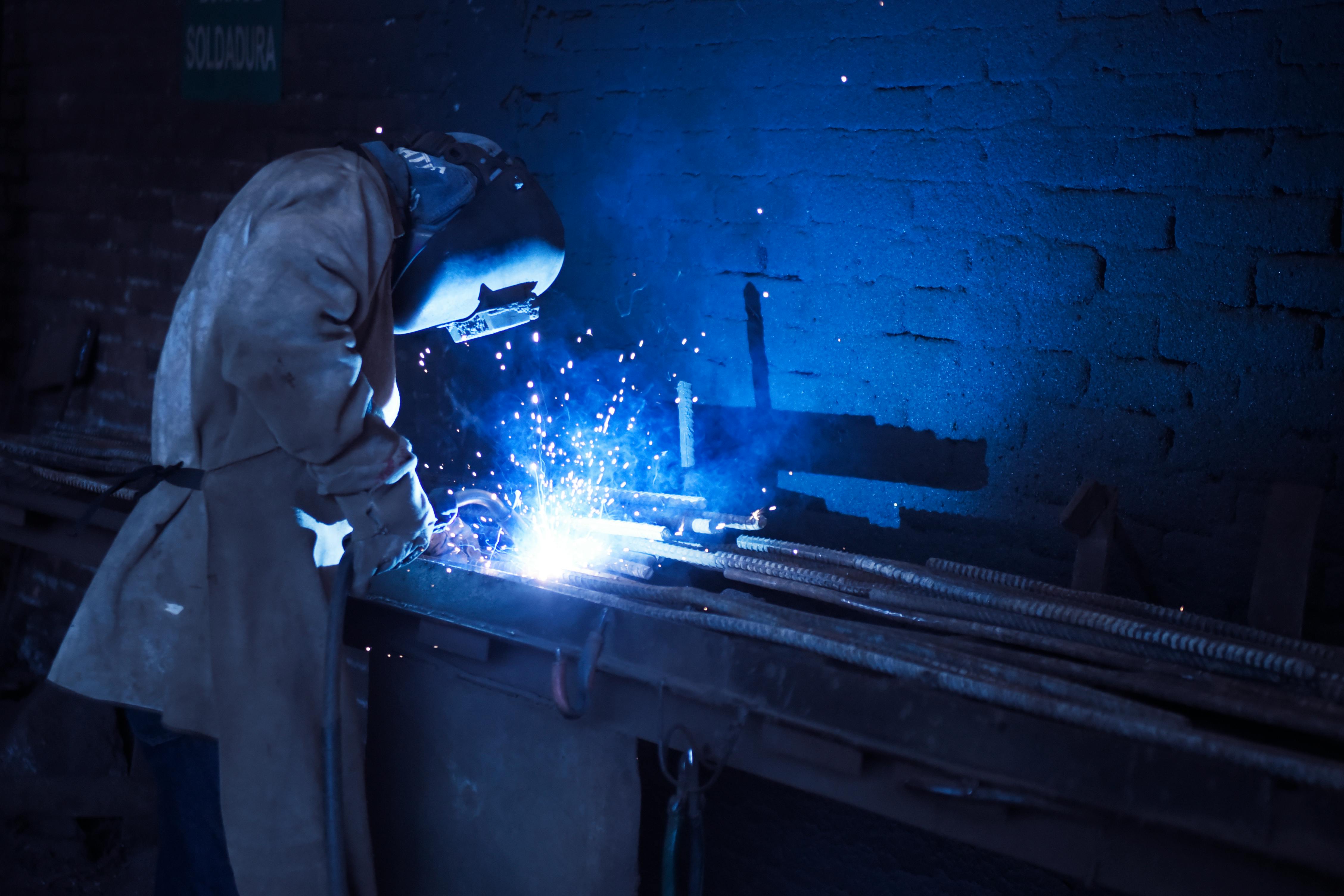
Thomas Reynolds
Thomas is a certified welding instructor with over 20 years of experience in the welding industry. He specializes in stick welding techniques and has trained hundreds of professional welders throughout his career. Thomas regularly consults with manufacturers on the design and improvement of stick welders for both industrial and consumer applications.