发布日期: 2025年1月12日 • 阅读时间: 10分钟
Engine Driven Welders: The Ultimate Power Solution for Remote Welding
A comprehensive guide to choosing, using, and maximizing performance of engine driven welders for professional applications
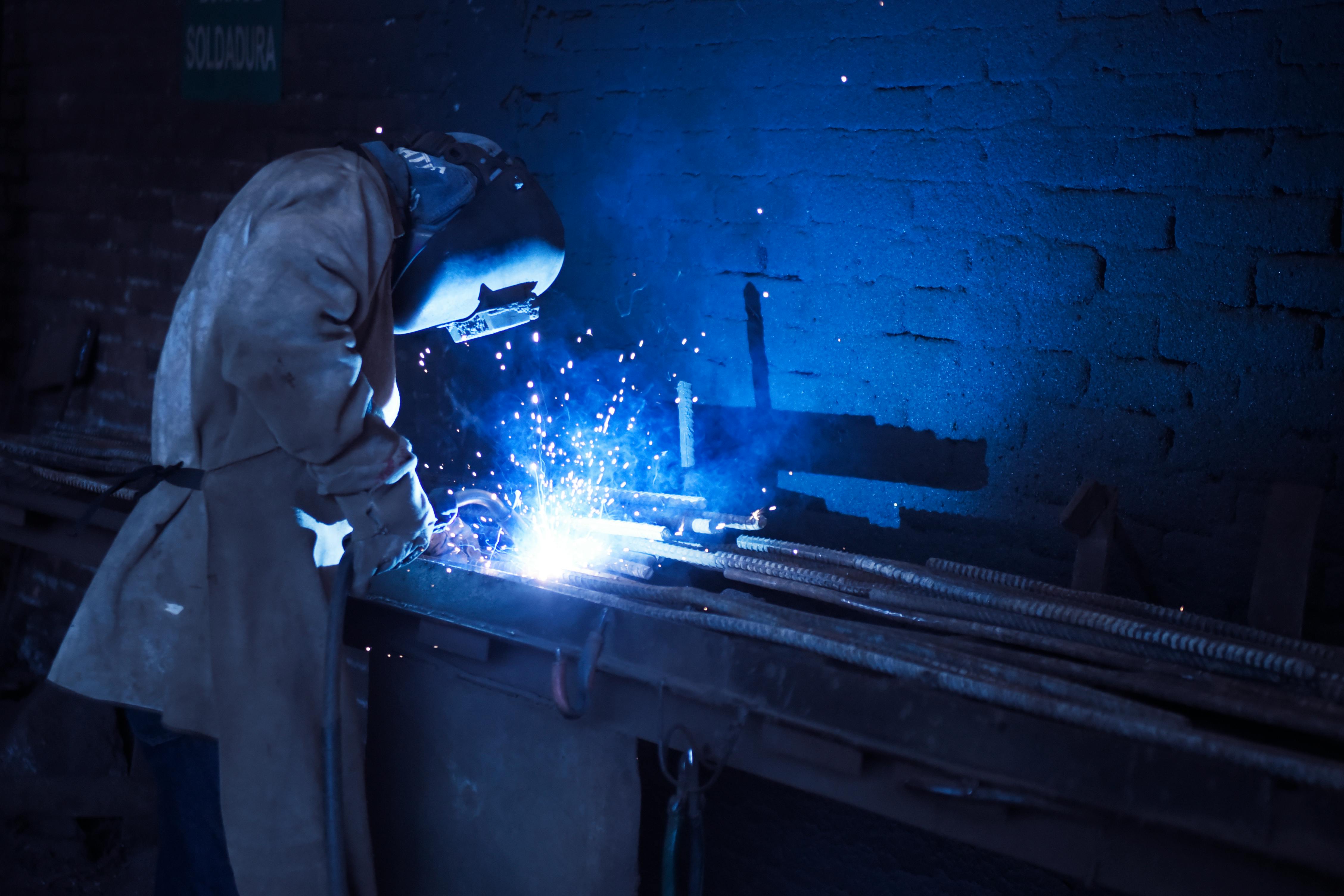
Understanding Engine Driven Welders: Power and Portability Combined
Engine driven welders represent the pinnacle of portable welding technology, combining robust power generation with advanced welding capabilities. Unlike conventional welding machines that require external electrical connections, engine driven welders integrate an internal combustion engine with a welding generator, creating a self-sufficient welding power solution. This makes engine driven welders indispensable tools for professionals working in remote locations, construction sites, pipeline projects, and emergency repair scenarios where grid power is unavailable or unreliable.
The market for engine driven welders has expanded significantly in recent years, with technological advancements enhancing performance, fuel efficiency, and versatility. Modern engine driven welders now offer sophisticated welding controls, multi-process capabilities, and auxiliary power options that transform these machines into complete mobile workstations. Understanding the core characteristics and applications of engine driven welders is essential for professionals seeking to maximize productivity in challenging environments.
Key Benefits of Engine Driven Welders
Complete Mobility
Engine driven welders provide true freedom from electrical grid constraints, enabling welding operations virtually anywhere a machine can be transported.
Dual Functionality
Most engine driven welders double as auxiliary power generators, providing electricity for tools, lights, and equipment alongside welding capabilities.
Robust Performance
Engine driven welders typically deliver more stable arc performance in demanding conditions compared to grid-dependent alternatives.
Types of Engine Driven Welders by Fuel Source
Engine driven welders are primarily categorized by the type of fuel they use, with each variant offering distinct advantages for specific applications. The choice of fuel source significantly impacts the performance characteristics, operational costs, and suitability of engine driven welders for different work environments. The following represents the main categories of engine driven welders available in the current market:
Gasoline Engine Driven Welders
Gasoline-powered engine driven welders are popular for their:
• Lower initial purchase cost among engine driven welders
• Lighter weight and enhanced portability
• Easier starting in moderate temperatures
• Widely available fuel source
• Simpler maintenance compared to other engine driven welders
• Ideal for contractors requiring frequent transportation of engine driven welders
Diesel Engine Driven Welders
Diesel-powered engine driven welders offer these advantages:
• Superior fuel efficiency for extended operation
• Greater durability and longer engine life
• Higher torque output for demanding applications
• Better performance in continuous duty scenarios
• Preferred for industrial applications of engine driven welders
• Lower fire hazard compared to gasoline engine driven welders
Propane/Natural Gas Engine Driven Welders
LP/NG engine driven welders provide these benefits:
• Cleaner burning with reduced emissions
• Lower fuel costs in many markets
• Extended runtime when connected to large tanks
• Reduced engine maintenance requirements
• Ideal for environmentally sensitive applications
• Some models of engine driven welders offer dual-fuel capability
Multi-Fuel Engine Driven Welders
The newest category of engine driven welders offers:
• Flexibility to operate on multiple fuel types
• Adaptation to fuel availability in remote locations
• Reduced operational constraints
• Innovative engine technology for engine driven welders
• Higher initial investment but greater versatility
• Increasingly popular in international and expedition applications
Engine Driven Welders Classified by Output Type
Beyond fuel type, engine driven welders are also differentiated by their electrical output characteristics, which determine the welding processes they can support. When selecting engine driven welders for specific applications, understanding these output classifications is crucial for matching the machine to your welding requirements. The primary output classifications for engine driven welders include:
Type of Engine Driven Welders | Welding Processes | Ideal Applications |
---|---|---|
CC (Constant Current) Engine Driven Welders | Primarily Stick/SMAW and TIG/GTAW welding | Pipeline work, structural steel, maintenance and repair with engine driven welders |
CV (Constant Voltage) Engine Driven Welders | Specialized for MIG/GMAW and Flux-Cored/FCAW | Manufacturing, sheet metal work, production applications of engine driven welders |
CC/CV Engine Driven Welders | Multi-process capability for all standard welding processes | Versatile applications requiring different processes; premium engine driven welders for contractors |
Advanced Process Engine Driven Welders | Specialized pulse capabilities, advanced arc control | High-end fabrication, aluminum welding, precision applications of engine driven welders |
The continuous advancement in engine driven welders technology has led to increasingly sophisticated machines that offer unprecedented versatility in the field. Modern engine driven welders often combine multiple output types with digital controls, enabling precise adjustment of welding parameters for optimal results across various materials and joint configurations. This evolution has transformed engine driven welders from basic power sources into advanced welding systems capable of meeting the most demanding professional applications.
Leading Manufacturers and Their Engine Driven Welders
The market for engine driven welders is dominated by several established manufacturers, each offering distinctive product lines with unique features and capabilities. Understanding the strengths and specializations of these leading engine driven welders brands can help professionals make informed purchasing decisions that align with their specific requirements. The following manufacturers represent the industry leaders in engine driven welders technology:
Lincoln Electric Engine Driven Welders
Lincoln Electric is renowned for their rugged and reliable engine driven welders, particularly:
• The Ranger® series of gasoline engine driven welders (180-250A)
• The Vantage® series of diesel engine driven welders (300-600A)
• Advanced multi-process capabilities in higher-end engine driven welders
• Chopper Technology® for superior arc performance
• Lincoln's engine driven welders are preferred in pipeline and structural applications
• Their engine driven welders feature digital control interfaces on premium models
Miller Electric Engine Driven Welders
Miller Electric offers innovative engine driven welders known for:
• The Bobcat™ series of compact engine driven welders
• The Trailblazer® series with advanced arc control
• The Big Blue® line of industrial diesel engine driven welders
• Exclusive Auto-Speed™ technology that optimizes engine RPM
• Excel™ power in select engine driven welders providing clean AC power
• Miller's engine driven welders are favored in maintenance and fabrication
ESAB Engine Driven Welders
ESAB's engine driven welders are distinguished by:
• The Warrior™ series of compact multi-process engine driven welders
• The Robust Feed wire feeders designed for engine driven welders
• Advanced digital interfaces on newer engine driven welders models
• Precision arc control technology
• Global service network supporting their engine driven welders
• Competitive pricing in the professional engine driven welders market
Hobart Engine Driven Welders
Hobart offers value-focused engine driven welders with:
• The Champion™ series of gasoline engine driven welders
• The Trek™ series designed for mobile applications
• Emphasis on reliability in their engine driven welders design
• Simplified controls for straightforward operation
• Strong dealer support network for engine driven welders
• Popular among small contractors and farm/ranch applications
Critical Technologies in Modern Engine Driven Welders
The technological innovation in engine driven welders has accelerated in recent years, with manufacturers introducing advanced features that enhance performance, efficiency, and usability. These technologies differentiate premium engine driven welders from basic models and can significantly impact productivity and weld quality in the field. When evaluating engine driven welders for purchase, the following technologies merit special consideration:
Advanced Technologies in Premium Engine Driven Welders
Intelligent Engine Management
Advanced <strong>engine driven welders</strong> feature dynamic engine control systems that automatically adjust engine speed based on power demand, reducing fuel consumption by up to 30% compared to conventional <strong>engine driven welders</strong> that run at constant speed.
Digital Welding Process Control
High-end <strong>engine driven welders</strong> now incorporate microprocessor-controlled welding circuits that optimize arc characteristics for specific applications, providing weld quality comparable to sophisticated shop-based welding power sources.
Clean Power Technology
Some premium <strong>engine driven welders</strong> feature advanced alternator designs and power conditioning circuits that deliver stable, clean auxiliary power suitable for sensitive electronics and computers, distinguishing them from basic <strong>engine driven welders</strong> with rudimentary power outputs.
Remote Monitoring and Diagnostics
The newest generation of <strong>engine driven welders</strong> incorporate telematics systems that enable remote monitoring of machine status, performance metrics, and maintenance requirements, optimizing fleet management of <strong>engine driven welders</strong> for large operations.
Performance Metrics for Evaluating Engine Driven Welders
When comparing different models of engine driven welders, several key performance metrics should be evaluated to ensure the selected machine meets specific project requirements. Understanding these specifications is essential for making informed decisions when investing in engine driven welders. The following parameters represent the most important performance indicators for engine driven welders:
Performance Metric | Description | Typical Range in Engine Driven Welders |
---|---|---|
Welding Output Range | The minimum and maximum amperage the engine driven welders can produce for welding applications | Small: 120-180A Medium: 180-300A Large: 300-600A |
Duty Cycle | The percentage of a 10-minute period that engine driven welders can operate at a specified amperage without overheating | 100% at rated output for premium engine driven welders 60% at maximum output for mid-range models |
Auxiliary Power Output | The amount of AC power engine driven welders can provide for tools and equipment | Small: 3-5 kW Medium: 5-10 kW Large: 10-20+ kW |
Fuel Efficiency | The operating time engine driven welders can achieve per gallon/liter of fuel | Varies by size and technology; advanced engine driven welders may achieve 8-10 hours per tank |
Beyond these core specifications, prospective buyers of engine driven welders should also consider factors such as noise levels (typically 70-80 dB for standard engine driven welders), weight (ranging from 300 to 1,500+ lbs depending on the class of engine driven welders), and physical dimensions. These factors can significantly impact the usability of engine driven welders in specific work environments, particularly when mobility and noise restrictions are important considerations.
Applications and Use Cases for Engine Driven Welders
Engine driven welders are deployed across a wide range of industries and applications where conventional power sources are impractical or unavailable. The versatility of modern engine driven welders has expanded their use beyond traditional construction and pipeline work into diverse sectors requiring mobile welding solutions. Understanding the primary applications of engine driven welders can help professionals determine whether these machines represent an appropriate investment for specific business requirements.
Construction and Infrastructure
Engine driven welders are fundamental in construction applications:
• Building structural frameworks where grid power isn't established
• Bridge construction and rehabilitation projects
• Infrastructure installation in developing areas
• Highway and transportation system repairs
• Using engine driven welders for reinforcement and structural components
• Mobile crews rely on engine driven welders for flexibility across large sites
Pipeline and Energy Sector
The pipeline industry is a primary user of engine driven welders:
• Oil and gas pipeline construction and maintenance
• Cross-country transmission lines requiring engine driven welders
• Remote wellhead repairs and modifications
• Energy infrastructure in isolated locations
• Emergency repairs during service interruptions
• Multiple engine driven welders coordinated for large-scale projects
Agricultural and Rural Applications
Farm and ranch operations benefit from engine driven welders:
• Maintaining agricultural equipment in the field
• Irrigation system installation and repairs
• Livestock handling facilities construction
• Farm infrastructure where engine driven welders provide both welding and power
• Remote property improvements beyond utility connections
• Engine driven welders serving as emergency backup power sources
Emergency Response and Disaster Recovery
Engine driven welders are critical in emergency situations:
• Post-disaster infrastructure stabilization
• Emergency utility restoration requiring engine driven welders
• Temporary structure assembly in disaster zones
• Search and rescue operations needing cutting/welding capability
• Mobile command posts powered by engine driven welders
• Rapid response teams deploying engine driven welders for multiple functions
Maintenance and Operational Considerations for Engine Driven Welders
The reliability and longevity of engine driven welders depend significantly on proper maintenance and operational practices. Unlike shop-based welding power sources, engine driven welders have internal combustion engines that require specific care routines to ensure optimal performance. Implementing a comprehensive maintenance program for engine driven welders can prevent costly downtime and extend service life. The following represents essential maintenance considerations for engine driven welders:
Essential Maintenance Schedule for Engine Driven Welders
Daily Checks for Engine Driven Welders
- Check engine oil level and condition
- Inspect coolant level (water-cooled models)
- Examine air filter indicator
- Verify fuel supply and quality
- Inspect welding cables and connections
Monthly Maintenance for Engine Driven Welders
- Change engine oil and filter
- Clean or replace air filter elements
- Inspect and clean radiator fins
- Check battery condition and connections
- Inspect all belts for tension and wear
Annual Service for Engine Driven Welders
- Replace fuel filters
- Change coolant and flush system
- Clean and test fuel injectors
- Perform engine valve adjustments
- Test all safety systems and controls
Operational Best Practices for Engine Driven Welders
Beyond routine maintenance, the way engine driven welders are operated significantly affects their performance and service life. Implementing operational best practices can maximize the efficiency and reliability of engine driven welders while minimizing wear and fuel consumption. Operators of engine driven welders should be trained in the following practices to ensure optimal machine performance:
Operating Efficiency Practices
- Allow proper warm-up time for <strong>engine driven welders</strong> before applying welding loads
- Use idle control features when available on <strong>engine driven welders</strong> to reduce fuel consumption
- Match generator power output to actual requirements rather than running <strong>engine driven welders</strong> at maximum output
- Position <strong>engine driven welders</strong> to optimize air flow and prevent overheating
Safety and Performance Considerations
- Never operate <strong>engine driven welders</strong> in enclosed spaces without proper ventilation
- Ensure <strong>engine driven welders</strong> are properly grounded according to manufacturer specifications
- Avoid running <strong>engine driven welders</strong> with low fuel to prevent air in the fuel system
- Monitor <strong>engine driven welders</strong> for unusual noise, vibration, or operational changes
Purchasing Guide for Engine Driven Welders
Selecting the right engine driven welders for specific business needs requires careful consideration of multiple factors beyond basic specifications. With investments in quality engine driven welders ranging from $3,000 to $15,000+, making an informed purchasing decision is essential for maximizing return on investment. This comprehensive buying guide outlines the key considerations when evaluating engine driven welders for purchase.
Key Factors in Selecting Engine Driven Welders
Application Requirements
Carefully assess your specific welding needs:
• Primary welding processes required
• Typical material types and thicknesses
• Required duty cycle for your applications
• Auxiliary power needs beyond welding
• Mobility requirements for your engine driven welders
Total Cost of Ownership
Look beyond the purchase price of engine driven welders:
• Fuel efficiency and operational costs
• Maintenance requirements and parts availability
• Warranty coverage and terms
• Expected service life of engine driven welders
• Resale value of premium engine driven welders
Support and Service
Consider the support ecosystem for engine driven welders:
• Local dealer support availability
• Manufacturer training and resources
• Service technician accessibility
• Parts availability for your model
• User community and knowledge sharing
Recommended Engine Driven Welders by Application Type
Based on extensive field experience and performance analysis, certain engine driven welders are particularly well-suited for specific applications. While individual requirements may vary, the following recommendations provide a starting point for selecting engine driven welders that align with common usage scenarios:
Application | Recommended Engine Driven Welders | Key Features to Look For |
---|---|---|
Construction Contractor | Mid-sized gasoline engine driven welders (250-300A) with multi-process capability | Portability, multi-process capability, sufficient auxiliary power for tools |
Pipeline Operations | Large diesel engine driven welders (300-500A) with advanced arc control | High duty cycle, specialized pipe welding programs, robust design for harsh conditions |
Farm/Ranch Use | Compact engine driven welders (180-250A) with good auxiliary power | Reliability, ease of maintenance, good stick welding performance, AC power for tools |
Mobile Repair Service | Truck-mounted engine driven welders with integrated air compressors | Compact design, multi-functionality, reliability, ease of operation |
Conclusion: The Future of Engine Driven Welders
Engine driven welders continue to evolve with emerging technologies and changing industry requirements. The future development of engine driven welders is likely to focus on several key areas: increased fuel efficiency, reduced emissions, enhanced digital controls, and improved integration with other systems. As environmental regulations become more stringent, manufacturers of engine driven welders are investing in cleaner technologies while maintaining the power and reliability that professionals depend on.
For welding professionals and businesses that operate in remote locations or require mobile welding capabilities, engine driven welders remain an essential investment. By carefully evaluating specific application requirements, operational considerations, and long-term costs, buyers can select engine driven welders that deliver optimal performance and value. While the initial investment in quality engine driven welders may be substantial, the operational flexibility and productivity benefits they provide make them indispensable tools for many welding operations.
Whether supporting critical infrastructure projects, enabling agricultural operations, or providing emergency response capabilities, engine driven welders continue to play a vital role in modern industrial applications. As technology advances, these versatile machines will further cement their position as essential equipment for professionals who need reliable welding power and auxiliary electricity in challenging environments.
Our team of welding experts can provide personalized recommendations based on your specific application requirements, budget considerations, and operational constraints.
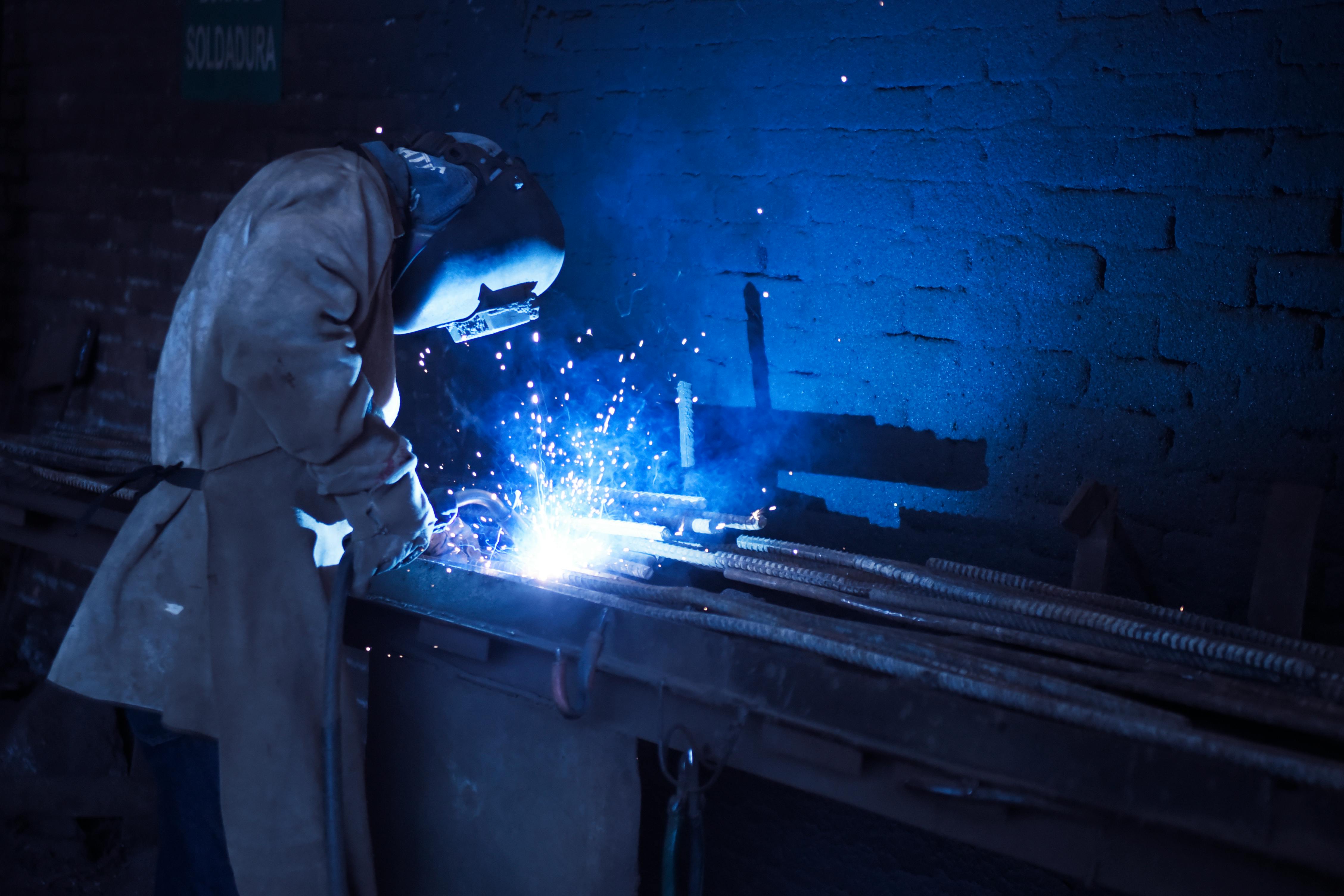
James Wilson
James is a certified welding inspector and equipment specialist with over 15 years of experience testing and evaluating welding equipment. He has extensive field experience with engine driven welders across pipeline, construction, and emergency response applications.